生產過程中發生的急性硫化氫中毒
生產過程中的硫化氫一般是某些化學反應的產物,或以雜質形式存在。如染料合成、催化劑合成和化學纖維制造中有些工藝會產生硫化氫,石油加工、煤氣制造中的脫硫過程中也會產生硫化氫,這些企業是急性硫化氫中毒事故的多發企業。因此,企業應當把防止急性硫化氫中毒事故作為職業衛生和安全工作的重點之一。
實例1 1983年12月30日,某染料化工廠分散蘭車間硫化堿工段,大學畢業剛進廠尚未分配工作的洪某來到該工段勞動,工作中硫化堿工段長高某見硫化堿沉降槽發生堵塞現象,便用大量的水沖洗硫化堿沉降槽,沖洗后的廢液流入了硝酸廢液貯槽內,立即發生酸堿中和反應,產生了大量的硫化氫氣體。并迅速逸入工段內,洪某和高某因吸入過量硫化氫氣體而引起急性硫化氫中毒,另一名工人發生硫化氫吸入反應。1988年6月2日上午9時左右,另一家染料化工廠1012工段深紅色基RC染料精制崗位,操作工楊某將6桶粗料(包括從陰溝和地上清掃收集的回收料)投入精制桶內,加入鹽酸升溫溶解。由于粗料中混有硫化堿,在升溫溶解過程中發生化學反應,產生大量硫化氫氣體,楊某吸入高濃度硫化氫氣體昏倒在地,經醫務室醫務人員緊急處理后,送入醫院搶救脫險,醫院診斷為急性重度硫化氫中毒。
兩起中毒事故均發生在染料化工廠,主要原因是企業管理松懈,缺乏職業衛生和安全操作規程,作業工人自我保護意識淡薄。硫化堿遇酸會產生硫化氫,應該是染料化工廠的常識,然而,操作工人不管是沖洗硫化堿沉降槽,還是粗料加酸升溫精制,明知存在產生硫化氫危險,仍然不采取任何防范措施,結果導致硫化氫大量產生并迅速逸出,當事人猝不提防,吸入過量硫化氫氣體而中毒。
實例2 1984年8月11日上午11時左右,某電化廠三車間二硫化碳工段,曹某等6名農民工在鼓風機房內從事酸劑油化作業時,鼓風機房因故停電,用于排除硫化氫廢氣的鼓風機突然停止運轉,致使大量硫化氫氣體從風機口倒灌至酸劑油化作業操作場所,在場的6名農民工均因吸入高濃度硫化氫而引起急性硫化氫中毒,其中曹某等4人當即昏迷、呼吸停止、瞳孔散大,病情十分危急,幸好現場救援及時,將病人迅速送入醫院搶救脫險。
將排除硫化氫廢氣的鼓風機房用作酸劑油化作業場所,本身就很不恰當,因為一旦出現意外發生硫化氫泄漏,酸劑油化作業工人首先將無辜受害。另外,排風的動力系統發生故障會引起硫化氫氣體倒灌,在設計時就應考慮排風系統的電源與生產設備連動,同步啟動工作,關閉時則最好先關生產設備,后關排風系統。為防止意外,排風系統還可采用兩路電源供電的方法,一條電路故障時能自動切換另一條電路。
實例3 1994年2月28日,本市某焦化總廠三聯供脫硫工段,某市政工程公司工程處工人陳某和于某在下水道進行清理作業。兩人剛作業15分鐘左右,即感到煩燥、胸悶,繼而呼吸急促、神志不清,昏倒在地。經現場急救,給予吸氧后送入醫院治療,醫院診斷為急性重度硫化氫中毒。現場測定結果,硫化氫濃度為100mg/m3,超過國家衛生標準9倍。
經調查,該焦化總廠脫硫工段熔硫釜的放散管在放散硫化氫氣體時,硫化氫氣體進入了水封設備中,水封設備水滿后流入下水道,硫化氫氣體隨之流入下水道,造成清理下水道的工人發生硫化氫中毒。事故的原因主要是設備布置不合理,致使生產過程中產生的硫化氫氣體逸入了下水道,同時,事故的發生也說明企業管理松懈,缺乏職業衛生和安全操作規程,作業工人自我保護意識淡薄。下水道作業本身就是硫化氫中毒高發作業,作業前應采取相應的防范措施,可是作業者不使用個人防護用品便進行作業,結果引起硫化氫中毒。
實例4 某煤氣廠于1997年9月份進行系統大修,9月1日上午停車,先用氮氣對甲醇車間管道進行置換吹掃,9月2日上午9時左右,陳某等兩名工人在D105閃蒸器出口(直徑300mm)進行墻盲板作業,在盲板插進后,陳俯臥在地觀察盲板位置是否擺正,此時從尚未擰緊螺栓的管道內沖出一股硫化氫氣體,陳某不慎吸入后即刻中毒昏倒在地,現場監護人員發現后立即將其抬離現場,送入醫院急救脫險。
煤氣制造過程中存在硫化氫氣體,進行系統大修,特別要防止硫化氫、一氧化碳等有害氣體的危害。因此大修前應制訂相應的職業衛生和安全操作規程,并嚴格監督執行。本事故的發生,就是事先沒有采取防范管道內有害氣體逸出的措施所致。
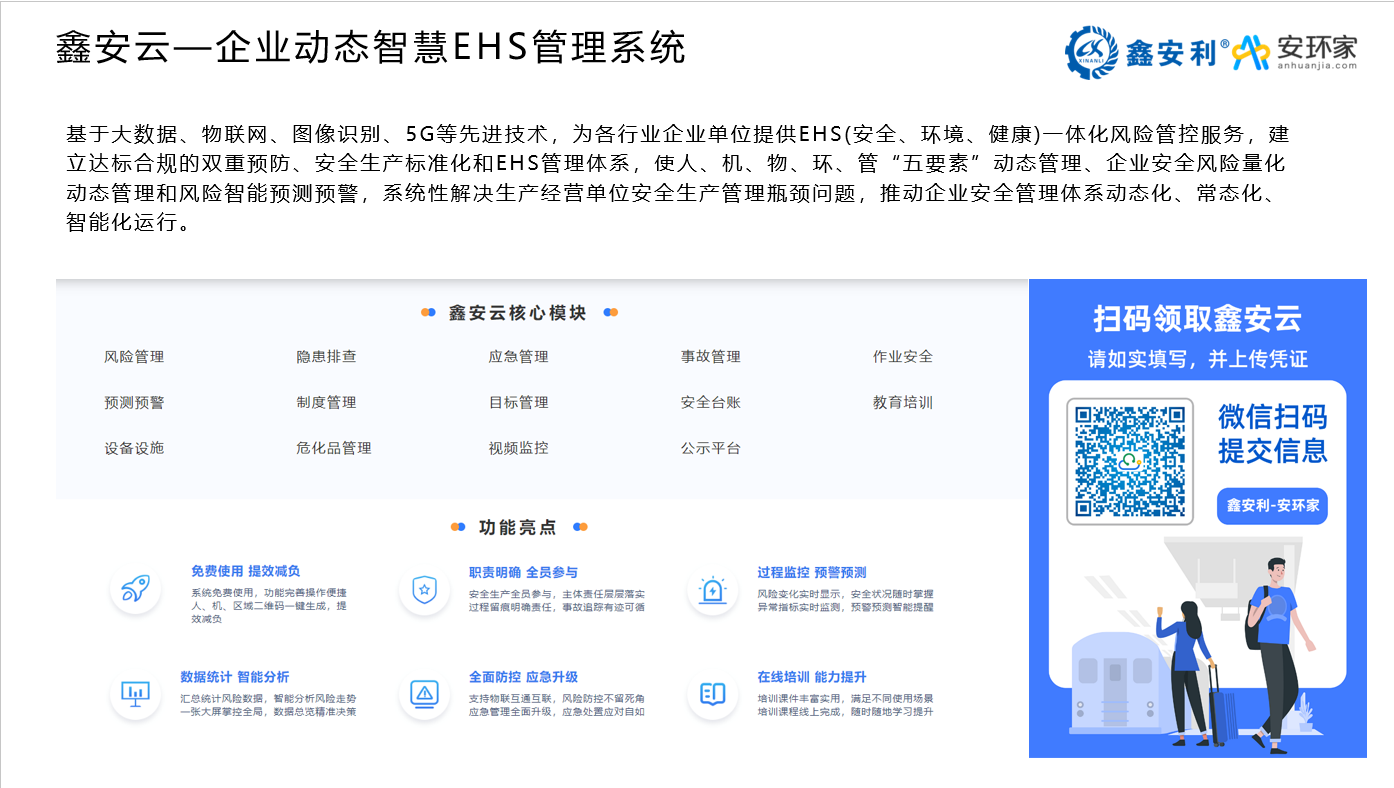