當前,我國化學工業(yè)正向著多樣化、大型化、連續(xù)化、自動化的趨勢發(fā)展。
1.化工產(chǎn)品和生產(chǎn)方法的多樣化
化工生產(chǎn)所用的原料、半成品、成品種類繁多,絕大部分是易燃、易爆、有毒性、具腐蝕的化學危險品。而化工生產(chǎn)中一種主要產(chǎn)品可以聯(lián)產(chǎn)或副產(chǎn)幾種其它產(chǎn)品,同時,又需要多種原料和中間體來配套。同一種產(chǎn)品往往可以使用不同的原料和采用不同的方法制得。如苯的主要來源有四個:煉廠副產(chǎn)、石腦油鉑重整、裂解制乙烯時的副產(chǎn)以及甲苯經(jīng)脫烷基制取苯。而用同一種原料采用不同的生產(chǎn)方法,可得到不同的產(chǎn)品。如從化工基本原料乙烯開始,可以生產(chǎn)出多種化工產(chǎn)品。
2.生產(chǎn)規(guī)模的大型化
解放以前,我國的化學工業(yè)十分落后,以化肥為例,只有大連、南京兩家工廠,合成氨年產(chǎn)量不過萬噸左右,其它如酸堿、油脂,染料等行業(yè)工廠規(guī)模很小,有的僅是作坊,化工產(chǎn)品基本依賴進口。
建國以后,經(jīng)過三年恢復和第一個五年計劃建設,我國化學工業(yè)像其它產(chǎn)業(yè)一樣,得到了恢復和發(fā)展。20世紀50年代,吉林、蘭州、太原、成都等地都相繼建立了年產(chǎn)2.5萬噸級的合成氨廠,60年代又在浙江衢縣、上海吳涇等地建成了20多個中型氮肥廠。在此期間,我國著名化工專家侯德榜先生開創(chuàng)了碳酸氫銨新工藝,簡化了氮肥生產(chǎn)過程,使其具備了普及條件。幾年間,中小化肥廠在全國遍地開花,不僅培養(yǎng)了大批化工人才,而且產(chǎn)量也構成與大中型化肥相匹敵的能力。從70年代開始我國從國外引進了日產(chǎn)千噸合成氨以及相配套的大型尿素裝置,目前已建成了許多年產(chǎn)30萬t合成氨的大型化肥裝置。以合成氨計算,從1970~1985年,產(chǎn)量增長了7倍。
石油化工的發(fā)展代表一個國家的化學工業(yè)水平。我國早期的石化工業(yè)主要靠石油煉制廠廢氣作原料,50年代蘭州化學工業(yè)公司合成橡膠廠就是用蘭州煉油廠的廢氣作原料的,后來,又生產(chǎn)酒精和聚苯乙烯。當時石油煉廠與石化工廠只是部分原料的供應關系。由于乙烯在煉廠廢氣中只占14%~15%,作為原料供不應求,世界各國出現(xiàn)了以煉廠石腦油和天然氣凝析液為原料。采用烴類裂解技術制造乙烯的大型石化工廠,生產(chǎn)乙烯的裝置也由20世紀50年代的lOkt級一躍而為100~300kt級。
化工裝置的大型化,在基建投資和經(jīng)濟效益上是無可爭辯的。以基建而論,由于化工裝置大部分是由塔。槽、釜、罐等設備構成,而投資額與容器設備的表面積成正比,產(chǎn)量則與其容積成正比,這樣產(chǎn)量越大而投資越少,促進了裝置的大型化。
從經(jīng)濟效益來看,大型化能夠合理利用原材料,降低消耗定額,減少操作人員以及相對
的后勤支援和公用工程的投資。
但是大型化也存在著設備制造,搬運,安裝條件等限制,以及大量原料貯存和處理的
困難。從安全角度考慮,大型化會帶來重大的潛在危險性。
(1)加工能量大增加了能量外泄的危險性
化工生產(chǎn)所用的原材料,多半本身就是能源或毒性源。加工過程中一旦外泄,就會燃燒爆炸或產(chǎn)生易爆的蒸氣云團或毒氣云,給人民財產(chǎn)帶來巨大的災難。1974年英國Flixborough地區(qū)化工廠己內(nèi)酰胺原料環(huán)己烷泄漏發(fā)生的蒸氣云爆炸和1984年印度博帕爾發(fā)生的異氰酸甲酯泄漏所造成的中毒事故,都是震驚世界的化學災害事故。
(2)單線生產(chǎn)更為普遍
大型化為了提高經(jīng)濟效益,則把各種生產(chǎn)有機地聯(lián)合起來,一個廠的產(chǎn)品就是另外一個廠的原料,輸入輸出只是在管道中進行,多數(shù)裝置直接接合,形成直線連接,不僅規(guī)模變大而且更為復雜,裝置間的相互作用強了,獨立運轉成為不可能。直線連接又容易形成許多薄弱環(huán)節(jié),使系統(tǒng)變得非常脆弱。
(3)生產(chǎn)彈性減弱
放棄了中間貯存設備,使彈性生產(chǎn)能力日益減弱。過去化工生產(chǎn)往往在工序或車間之間,設置一定的貯存能力,以調節(jié)生產(chǎn)的平衡,大型化必然帶來連續(xù)化和自動控制操作,不可能也不必要再設置中間貯存能力,但因此也導致生產(chǎn)彈性的減弱。
(4)控制集中化和自動控制,使系統(tǒng)復雜化
沒有控制的集中和自動化也談不上大型化。但控制設備和計算機也有一定的故障率,如果是開環(huán)控制,人是子系統(tǒng)的一員,人的低可靠性增大了發(fā)生事故的可能。
(5)設備條件要求日益嚴格
工廠規(guī)模大型化以后,對工藝設備的處理能力,材質和工藝參數(shù)要求更為提高。如輕油裂解、蒸汽稀釋裂解的裂解管壁溫要求都在900℃以上,合成氨,甲醇,尿素的合成壓力要求都在lOOatm以上,高壓聚乙烯壓縮機出口壓力為3500atm,高速水泵轉速達250.00r/m,天然氣深冷分離在—120~130℃的條件下進行,這些嚴酷的生產(chǎn)條件,給設備制造帶來極大的難度,同時也增加了潛在危險性的嚴重程度。
(6)大型化給社會帶來威脅
工廠大型化基本上是在原有廠區(qū)上逐漸擴建的,大量職工的生活需求又使廠區(qū)與居民區(qū)越來越近,一旦發(fā)生事故,便會對社會造成巨大影響。
3.工藝過程的連續(xù)化和自動控制
化工生產(chǎn)有間歇操作和連續(xù)操作之分,間歇操作的特點是各個操作過程都在一組或一個設備內(nèi)進行,反應狀態(tài)隨時間而變化,原料的投入和產(chǎn)出都在同一地點,危險性原料和產(chǎn)品都在崗位附近。因此,很難達到穩(wěn)定生產(chǎn),操作人員的注意力十分集中,勞動強度也很大,這就容易發(fā)生事故。間歇生產(chǎn)方式不可能大型化。連續(xù)化和自動控制是大型化的必然結果。
連續(xù)操作的特點是各個操作程序都在同一時間內(nèi)進行,所處理的原料在工藝過程中的任何一點或設備的任何斷面上,其物理量或參數(shù)(如溫度、壓力、以及濃度、比熱、速度等)在過程的全部時間內(nèi),都要按規(guī)定要求保持穩(wěn)定。這樣便形成了一個從原料輸入、物理或化學處理、形成產(chǎn)品的連續(xù)過程,原料不斷輸入,產(chǎn)品不斷輸出,使大型化成為可能。
連續(xù)大型化的生產(chǎn)很難想象能用人工控制。20世紀50年代中在某些化工生產(chǎn)中使用負反饋的定值控制方式,使工藝過程比較平穩(wěn),后來隨著工藝技術的發(fā)展,逐步進入了集中控制、自動控制和計算機控制,實現(xiàn)了工藝過程控制的自動化,保證了運轉條件和產(chǎn)品質量的穩(wěn)定,同時也提高了生產(chǎn)的安全性。
連續(xù)化生產(chǎn)的操作比起間歇操作要簡單,特別是各種物理量參數(shù)在正常運轉的全部時間內(nèi)是不變的;不像間歇操作不穩(wěn)定,隨時間變化經(jīng)常出現(xiàn)波動。但連續(xù)化生產(chǎn)中外部或內(nèi)部產(chǎn)生的干擾非常容易侵入系統(tǒng),影響各種參數(shù)發(fā)生偏離;由于各子系統(tǒng)的輸入輸出是連續(xù)的,上游的偏離量很容易傳遞到下游,進而影響系統(tǒng)的穩(wěn)定。連續(xù)化生產(chǎn)裝置和設備之間的相互作用非常緊密,輸入輸出問題也間歇操作復雜,所以必須實現(xiàn)自動控制,才能保持穩(wěn)定生產(chǎn)。自動控制雖然能增加運轉的可靠性,提高產(chǎn)品質量和安全性,但也不是萬無一失的。美國石油保險協(xié)會曾調查過煉油廠火災爆炸事故原因,其中因控制系統(tǒng)發(fā)生故障而造成的事故即達6.1%,所以即使采用自動控制手段,也應加強管理,搞好維護,不可掉以輕心。
4.間歇操作仍是化工生產(chǎn)的主要方式
間歇操作的特點是所有操作階段都在同一設備或地點進行。原料和觸媒、助劑等加入反應器內(nèi),進行加熱、冷卻、攪拌等操作,使之發(fā)生化學反應。經(jīng)一段時間反應完成后,產(chǎn)品從器內(nèi)全部或部分卸出,然后再加入新原料周而復始地進行新一輪的操作。
間歇操作適于生產(chǎn)批量較少而品種較多的化工產(chǎn)品,如染料、醫(yī)藥、精細化工等產(chǎn)品。這種生產(chǎn)方式仍是化工生產(chǎn)的重要方式之一。有些集中控制或半自動控制的化工裝置也還殘留著間歇操作的部分特性。
進行間歇操作時,由于人機接合面過于接近,發(fā)生事故很難躲避,崗位環(huán)境不良,勞動強度也大。因此,在中小型工廠中,如何改善間歇操作的安全環(huán)境和勞動條件,仍是當今化工安全的主攻方向。
5.生產(chǎn)工藝參數(shù)苛刻
采用高溫、高壓、深冷、真空等工藝參數(shù),可以提高單機效率和產(chǎn)品收率,縮短產(chǎn)品生產(chǎn)周期,使化工生產(chǎn)獲得更大的經(jīng)濟效益。然而,與此同時,也對工藝操作提出更為苛刻的要求,首先對設備的本質安全可靠性提出了更高的要求,否則,就極易因設備質量問題引發(fā)設備安全事故;其次,是要求操作人員必須具備較為全面的操作知識和高度的責任心,良好的技術素質和高度的責任心成為現(xiàn)代化工操作工的基本條件;最后,苛刻的工藝條件要求必須具備良好的安全了防護設施,以防工藝波動、誤操作等導致的事故,而對這些苛刻條件下的生產(chǎn)進行防護,無論從軟件,還是到硬件都不是一件很容易的事情。而一旦不能做好,就會發(fā)生不可估量的事故。
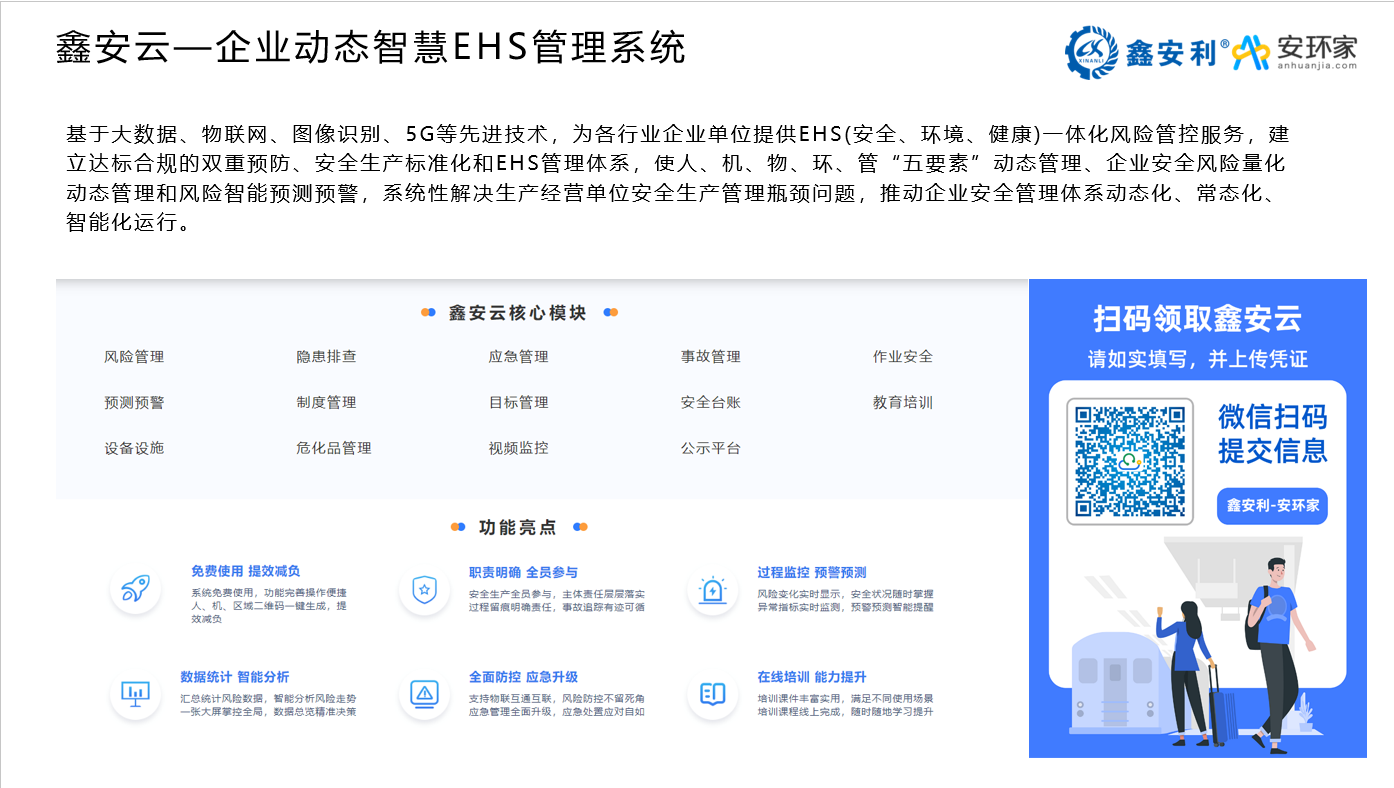