石油化工生產設備常年處于高溫高壓和各種腐蝕物的影響之下,由于設備的使用時間(老化狀況)、材料失效機理(如腐蝕、疲勞、沖蝕、應力效應等)、檢驗與維護保養的有效性等因素,設備往往會出現一些損壞狀況,比如凹坑、壁厚減薄、破裂、斷裂等,這些都會威脅企業的安全生產。但設備是在密封的狀態下運行,其受損情況很難準確掌握。該修的不修,肯定會影響安全生產,不必要修的修了,也會造成很大的浪費。
如何及時準確地掌握設備運行情況,以便采取必要的措施來確保設備的安全運行,國內外石化企業對此都十分重視。為了能夠更有效地評價設備損壞對安全的影響,1993年美國石油協會聯合20多家國際大型企業(作為項目贊助人)委托挪威船級社開發相關的評價技術。經過幾年的研究和探索,該協會于1998年正式推出RBI(基于風險的檢驗)評價方法,并編制了相關規范供各企業參考。至今RBI評價方法已在世界各國廣泛應用,效果比較顯著。
RBI是在追求系統安全性與經濟性統一的理念基礎上建立起來的一種優化檢驗策略的方法。它是在對所評估設備的潛在損傷機理、失效模式、失效概率、失效后果等進行科學分析的基礎上,對設備進行風險排序,找出主要問題與薄弱環節,制定合理的檢驗計劃,并通過實施檢驗和一定的風險減緩措施將設備風險降至期望水平,確保本質安全,減少運行的費用。
具體來說,它是采用先進的軟件,配合以豐富的工廠實踐經驗和腐蝕及冶金學方面的知識及經驗,對煉油廠、化工廠等工廠的設備、管線進行風險評估及風險管理方面的分析。根據分析的結果提出一個根據風險等級制定的設備檢測計劃。其中包括:會出現何種破壞事故;哪些地方存在著潛在的破壞可能;可能出現的破壞的頻率;應采用什么正確的測試方法進行檢測等。并可對現場人員進行培訓來正確實施、成功完成這些檢測工作。由于有了“有的放矢”的科學的檢測計劃,從而保證了企業安全、可靠的運行及取得最好的經濟效益。
在這個基礎上,運行的實施及管理成為科學、透明、可預見的。工廠設備的維護維修也由機械的、人為地安排,轉為按設備、設施、運行的薄弱環節及風險管理做出科學的安排。這就消除了一些不必要的停機維護或延長維修周期,使得企業的生產、設備在風險管理下可控制、可預見地運行。應用此項技術還可以避免因對裝置狀況不明、盲目使用所帶來的風險,以及避免因過度檢驗維修所造成的浪費。國內很多石化企業已經開始應用此項技術。
大慶石化公司煉油廠于2005年11月起在該廠的第一重油催化裝置采用RBI技術,多次對錄入的數據和初步計算結果進行討論、調整,使評估的結果更符合裝置的實際情況,從而明確了這一裝置設備及管道風險分布的情況和成因,并進行了風險排序。在此基礎上提出了降低風險的措施,并根據此次評估結果做出了該套裝置可延期一年檢修的重要建議,由此相應地降低了裝置檢修的費用,增加了企業效益。
實施及完成RBI技術,要求有一支知識淵博、實踐經驗豐富的專門技術人員隊伍和一個高水平的計算機軟件系統。
RBI技術的實施是一個長期的過程,包括分析階段、制定檢測計劃、實施RBI、對實施效果的檢查、審核、修正及提高。RBI分析是復雜而艱巨的工作,先進的軟件是需要的,但更需要的是一個包括設備專家、檢驗專家、腐蝕專家、工藝專家等組成的具有合作精神的團隊。把硬件設施、安全管理和設備損壞情況分開來評價,忽略了人員、設備、材料與環境各種因素的相互影響是不正確的。
“水能載舟,亦能覆舟”,一個完善的安全評價系統,可以協助企業對自身的安全生產狀況有更好的了解,從而采取有效的安全控制手段;然而,一個效果差的安全評價系統則往往會誤人誤事,忽略安全薄弱環節,積累很多的事故隱患,并且可能白白浪費了企業的資源。所以在應用RBI的過程中,企業應該慎重選擇合作伙伴,采用切實有效的方法和技術。
只有完善的安全評價才能為我們的企業與社會創造更安全的環境,從而創造出更多的財富,帶給大家更優質的生活。
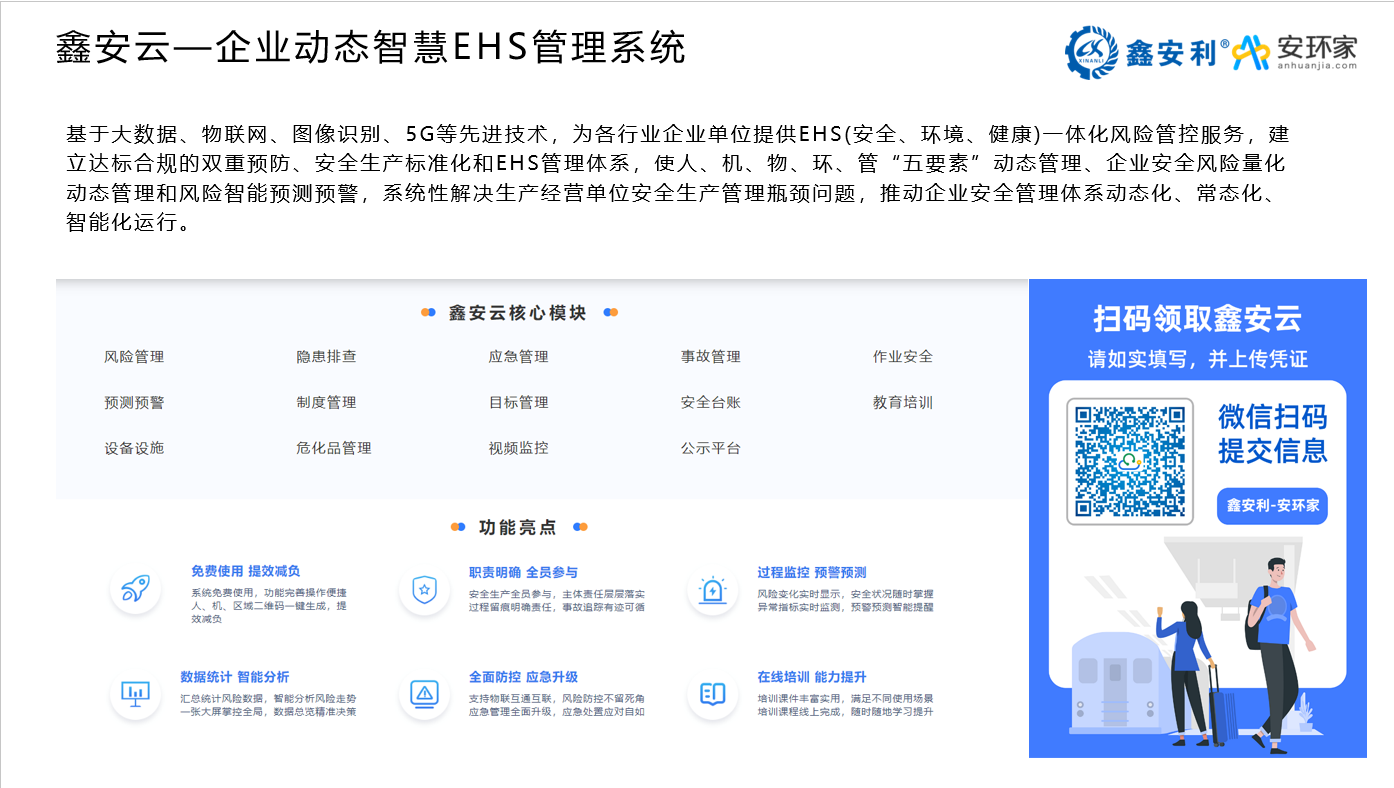