裝備的安全管理應該貫穿于裝備壽命周期的整個過程,即從設計、制造、安裝、試車、運行、維修直至退役的整個過程。
1 裝備的設計管理
1)石油化工裝備設計的管理程序
2)裝備設計的基本要求
(1)滿足生產性能要求;
(2)滿足可靠性要求:
(3)滿足維修性要求;
(4)滿足經濟性要求;
(5)滿足操作安全要求
(6)滿足其他要求
(7)應遵守國家和引進的有關設計標準和規定。特別是鍋爐、壓力容器,必須遵守有關的法規,如《鍋爐壓力容器安全監察規程》、GB150《鋼制壓力容器》、GB151《鋼制管殼式換熱器》、GB12337《鋼制球形儲罐》、JB4710《鋼制塔式容器》等。
2 裝備的制造管理
裝備制造管理工作的主要內容包括:生產技術準備、外購外協件管理、生產計劃的編制和執行、日程計劃和調度、裝配和調試,以及制造過程中的質量管理等等。
裝備制造準備工作主要包括以下幾個方面。
1)設計圖紙的工藝分析與審查
2)制定工藝方案
3)編制工藝文件
4)設計和制造工藝裝備
5)裝備的制造工藝
為保證石油化工裝備的質量,必須嚴格遵守國家行業的有關標準和法規。如壓力容器的制造應遵守GB150《鋼制壓力容器》的有關規定,焊接則應遵守JB4078《鋼制壓力容器焊接工藝評定》、JB4420《鍋爐焊接工藝評定》、JB4709《鋼制壓力容器焊接工藝規程》及鍋爐壓力容器焊工考試規則》等有關標準。
3 裝備的安裝工程管理
1)安裝工程計劃的編制
(1)編制安裝計劃的依據:
(2)計劃編制程序及安裝費用預算:
2)安裝計劃的實施
(l)裝備管理部門提出安裝工程計劃及安裝作業進度表。
(2)裝備的入庫、出庫、移裝等按有關規定執行。
(3)工藝技術部門負責提供安裝平面位置圖;裝備管理部門根據設計要求和有關規定負責提供基礎圖及施工技術要求;動力管理部門負責動力配套線和水、氣等管網路圖及施工技術要求;修建部門負責基礎施工;裝備管理部門安裝技術人員及基礎設計人員負責安裝技術指導,并有責任對現場施工質量提出意見。
(4)裝備安裝部門負責安裝工程的組織和協調工作,并具體實施裝備搬運、定位、找平、配電及配水管、氣管等工作(配管路、配電工作或由動力部門實施)。安裝質量的驗收由安裝部門提出,會同裝備管理部門(或調試單位)和使用部門共同進行。
(5)裝備的調試 一般裝備的調試工作(包括清洗、檢查、調整、試車)原則上由使用部門組織進行。精、大、稀、關裝備及特殊情況下的調試由裝備管理部門與工藝技術部門協同組織。自制裝備由制造單位調試,設計、工藝、裝備、使用部門參加。
(6)裝備調試的輔助材料(包括油料、清洗劑、擦拭材料等)其費用可在裝備安裝費專項內支付,一般零星安裝項目可在生產費用中攤銷,輔料的領用由使用部門負責。
(7)裝備安裝計劃的執行情況由裝備管理部門會同生產部門進行檢查。
3)裝備安裝工程的驗收
(1)裝備基礎的施工驗收由修建部門質量檢查員會同士建施工員進行驗收,填寫施工驗收單。基礎的施工質量必須符合基礎圖和技術要求,符合《裝備安裝基礎施工規范》。
(2)裝備安裝工程的最后驗收在裝備調試合格后進行,由裝備管理部門及安裝單位負責組織,檢查部門、使用部門等有關人員參加,共同做出鑒定,填寫有關施工質量、精度檢驗、試車運轉記錄等憑證和驗收移交單(見表3—12)。裝備管理部門主管領導簽“同意啟用”,使用部門負責人簽“同意接收”,方告竣工。
4)裝備安裝工程的費用管理
4 裝備的試車
試車工作一般可分為試車準備、模擬試車、投料試車與性能測試、報告確認等階段。圖3—15為試車過程示意圖。應該說明的是在整個過程中必須注重安全操作、安全檢查、事故處理、局部整改等各項工作。
5 裝備使用初期管理
使用初期管理的內容主要有:
(l)裝備初期使用中的調整試車,使其達到原設計預期的功能。
(2)操作工人使用維護的技術培訓工作。
(3)對裝備使用初期的運轉狀態變化觀察、記錄和分析處理。
(4)穩定生產、提高裝備生產效率方面的改進措施。
(5)開展使用初期的信息管理,制定信息收集程序,做好初期故障的原始記錄,填寫設備初期使用鑒定書及調試記錄等。
(6)使用部門要提供各項原始記錄,包括實際開動臺時、使用范圍、使用條件;零部件損傷和失效記錄;早期故障記錄及其他原始記錄。
(7)對典型故障和零、部件失效情況進行研究,提出改善措施和對策。
(8)對裝備原設計或制造上的缺陷提出合理化改進建議,采取改善性維修的措施。
(9)對使用初期的費用與效果進行技術經濟分析,并作出評價。
(10)對使用初期所收集的信息進行分析處理。
6 裝備運行安全管理
裝備經過試車和初期使用階段,即進入運行階段。在運行階段,一般應注意以下幾點:
1)定人定機制
2)操作證管理制
3)裝備操作維護規程
4)裝備使用崗位責任制
5)交接班制度
7 裝備的維護
1)日常維護(日常保養)
(1) 每班維護(每班保養)
(2)周末維護(周末保養)
2)定期維護(定期保養)
各類裝備的定期維護一般包含定期檢查的內容,主要有:
(1)拆卸指定的部件、箱蓋及防護罩等;徹底清洗裝備的外部;檢查及清洗裝備的內部。
(2)檢查、調整各部的配合間隙,緊固松動部位,更換巳磨損的易損件。
(3)疏通油路;增添油量;清洗或更換濾油器、油氈、油線;更換冷卻液;清洗冷卻液箱。
(4)清洗導軌等滑動面:清除毛刺;修正劃傷。
(5)清潔、檢查、調整電器線路及裝置(由維修電工負責)。
(6)排除故障,消除隱患。
通過定期維護后的裝備,要求達到:
(1)內外清潔,呈現本色;
(2)油路暢通,油標明亮;
(3)操作靈活,運轉正常。
3)使用維護上的特殊要求
8 裝備的檢查
1)裝備檢查的分類
(1)日常檢查
日常檢查
點檢:點檢內容一般以選擇對產品產量、質量、成本以及對裝備維修費用和安全衛生這五個方面會造成較大影響的部位為點檢項目較為恰當。如:
①影響人身或裝備安全的保護、保險裝置。
②直接影響產品質量的部位。
③在運行過程中需要經常調整的部位。
④易于堵塞、污染的部位。
⑤易磨損、損壞的零部件。
⑥易老化、變質的零部件。
⑦需經常清洗和更換的零部件。
⑧應力特大的零部件。
⑨經常出現不正常現象的部位。
⑩運行參數、狀況的指示裝置。為便于檢查,可以編制點檢卡,標明檢查項目內容、檢查方法、判別標準、檢查結果標記等。以做為檢查的依據,并做為檢查記錄。
(2)定期檢查
2)檢查記錄和報告
(1)裝備運行期間的檢查記錄
(2)裝備停運期間的檢查記錄
檢查報告應根據有關檢驗規程或主管部門的規定,按照規定的格式填報。現以壓力容器為例,國家勞動部《在用壓力容器驗驗規程》中規定了《在用壓力容器檢驗報告書》的統一格式。其中,對壓力容器檢查和檢驗包括以下15項報告內容:
(1)在用壓力容器檢驗結論報告;
(2)在用壓力容器原始資料審查報告;
(3)在用壓力容器內外部表面檢查報告及缺陷及缺陷部位圖(報告附錄);
(4)在用壓力容器壁厚測定報告;
(5)在用壓力容器磁粉探傷報告及探傷部位圖(報告附錄);
(6)在用壓力容器滲透探傷報告及探傷部位圖(報告附錄);
(7)在用壓力容器射線探傷報告及探傷部位圖(報告附錄);
(8)在用壓力容器超聲探傷報告及探傷部位圖(報告附錄);
(9)在用壓力容器化學成分分析報告;
(10)在用壓力容器硬度測定報告;
(11)在用壓力容器金相分析報告;
(12)在用壓力容器安全附件檢驗報告(一);
(13)在用壓力容器安全附件檢驗報告(二);
(14)在用壓力容器耐壓試驗報告;
(15)在用壓力容器氣密性試驗報告。
《在用壓力容器檢驗規程》規定凡從事該規程范圍內檢驗工作的檢驗單位和檢驗人員,應按勞動部頒發的《勞動部門鍋爐壓力容器檢驗機構資格認可規則》及《鍋爐壓力容器檢驗員資格鑒定考核規則》的要求,經過資格認可和鑒定的考核合格,方可從事允許范圍內相應項目的檢驗工作。檢驗單位應保證檢驗(包括缺陷處理后的檢驗)質量,檢驗時應有詳細記錄,檢驗后應出具《在用壓力容器檢驗報告書》。凡明確有檢驗員簽字的檢驗報告書必須由持證檢驗員簽字方為有效。表3—16為在用壓力容器射線探傷報告表。
9 裝備的維修(檢修)
1)檢修的基本方式
檢修主要有如下四種基本方式:
(1)事后維修(Breakdown Maintenance;簡寫為BM)
(2)預防維修(Preventive Maintenance;簡寫為PM)
(3)狀態監測維修(Condition-based Maintenance;簡寫為CBM)
(4)無維修設計(Design-out Maintenance;簡寫為DOM)
根據以上的分析,可歸納為如下的直觀結論:
①對劣化型故障的零部件來說,如更換容易,且維修費用低,最適用定期維修方式。
②對故障發生前有一個可以觀測的狀態發展過程的零部件來說,如更換難,且維修費用高,可采用監測維修。
③對維修費用很高的零部件,不管更換難易,都應考慮無維修設計。
④對不能或不必要進行預防維修或無維修設計的零部件,可采用事后維修方式。
⑤對頻頻發生故障的零部件,則需采用改善維修。
2)現行檢修體制
(1)大修理(簡稱大修), 它是計劃修理工作中工作量最大的一種修理。它以全面恢復裝備工作能力為目標,由專業修理工人進行。
(2)中修理(簡稱中修), 它是計劃修理工作中工作量介于大修和小修之間的一種修理。在中修時,須進行部分解體。這種修理類別目前于基本上為項修所替代。
(3)項目修理(簡稱項修,又稱針對性修理),它是根據裝備的實際技術狀態,對裝備精度、性能達不到工藝要求的某些項目,按實際需要進行針對性的修理。
在我國,項修已經逐漸取代了中修,而且在某種程度上這可以代替大修。
(4)小修理(簡稱小修),它是計劃修理工作中工作量最小的一種修理。
裝備大修、項修和小修工作內容比較列表如表3-18。
(5)年修理 石油化工企業中,除某些裝備仍需采用大、中(項)、小修外,其裝置裝備由于生產是每天24小時連續運行的,不允許稍或中斷,不允許發生故障停機,也就是要求有高度的可靠性。因此,對這種系統的裝置裝備需要在連續運行一年(約7000小時)進行一次年修理,稱為裝置停車大修理(簡稱年修理)。它是指對裝置中的大部分主要裝備同時進行大、中(項)修理。其工作內容有:對裝置中的大部分主要裝備和管道進行全面清洗、吹灰、除垢、檢查、檢測及零部件修理或更換。
(6)定期檢修 它是根據日常點檢和定期檢查中發現問題,拆卸有關的零部件,進行檢查、調整、更換或修復失效的零件,以恢復裝備的正常功能。其工作內容介于二級保養與小修之間。由于比較切合實際,因此目前已逐漸取代二級保養與小修。
3)檢修的技術管理
檢修技術管理工作包括:技術資料、質量標準、修后檢驗與服務等內容。
(1)裝備檢修的技術資料管理
裝備的技術資料是搞好裝備檢修和制造工作的重要依據,因此加強技術資料的管理至關重要。裝備維修用主要技術資料包括: 裝備說明書 ; 裝備維修圖冊 ; 各動力站裝備布置圖; 裝備修理工藝規程; 備件制造工藝規程; 專用工、檢、研具圖; 修理質量標準;裝備試驗規程; 其他參考技術資料。
(2)檢修質量標準
在制定裝備大修理質量標準時應遵循以下原則:
①以出廠標準為基礎。
②修后的裝備性能和精度滿足產品、工藝要求,并有足夠的精度儲備。
③對于整機有形磨損嚴重,或多次大修已難以修復到出廠精度標準的裝備,可適當降低精度要求,但應能滿足加工產品和工藝的要求。
④標準的內容主要包括,幾何精度、工作精度、外觀、空運轉試驗、負荷試驗及安全環保等方面的技術要求規定。其中勞動安全和環境保護則須達到有關法規的標準。
10 石油化工裝備的報廢與更新
11 壓力容器的使用和管理
由于壓力容器是一種特殊裝備,因此其使用和管理也有其特珠要求,加強企業壓力容器管理是確保企業安全生產的重要措施。
1)壓力容器的管理內容
裝備管理部門是壓力容器的主管部門,其主要職責有:
(1)貫徹執行國家勞動總局頒發的《壓力容器安全監察規程》;
(2)參加容器安裝的驗收及試運行工作;
(3)監督檢查壓力容器的運行、維修和安全裝置的校驗工作;
(4)根據容器的定期檢查周期,組織編制年、季度檢驗計劃,并負責組織實施;
(5)負責組織編制壓力容器的維護檢修規程和修理、改造、檢驗及報廢等技術審查工作;
(6)負責壓力容器的登記、編號、建擋及技術資料的管理和統計報表工作;
(7)參加壓力容器事故的調查、分析和上報工作,并提出處理意見和改進措施;
(8)負責組織檢驗人員、焊接人員、操作人員進行安全技術培訓和技術考核。
2)壓力容器的技術檔案管理
技術檔案管理是壓力容器管理的基礎工作,必須做到“齊全、及時、準確”。檔案內容除制造廠提供的原始檔案資料(包括設計資料、制造資料等)外,尚應包括:
(1)安裝、復驗、首檢記錄資料(首檢資料一般由各主管局壓力容器監督站提供)。安裝單位在移交給使用單位驗收時,應將設計、制造、首檢、安裝、復驗等有關資料一并移交。
(2)容器使用記錄應包括:①操作條件(壓力、溫度、介質特性等);②操作條件的變更。如壓力、溫度的波動范圍,間歇操作周期,工作介質特性的變化等;③開始使用日期,開停車日期,變更使用條件等;④壓力容器的檢查、修理記錄。包括檢驗或修理的日期、內容、結果、水壓試驗記錄,發現的缺陷以及處理情況等記錄。
3)壓力容器的安裝、使用、維護和檢修
壓力容器的安裝、使用、維護和檢修除要做到一般裝備的要求外,尚須做到以下各點:
(1)安裝壓力容器時應注意的事項
①無論是安裝在室外或室內,壓力容器的防火設施都應符合國家建筑設計及防火規范的要求;
②安裝在室外的壓力容器通風條件要好,同時還要考慮防日曬和防冰凍措施。安裝在室內的容器,其房屋必須寬敞、明亮、干燥,并保持正常溫度和良好的通風;
③室內務容器之間的距離不得小于0.75m,容器和柱之間的距離不得小于0.5m;
④居屋的室內標高決定于室內安裝容器的高度及吊裝要求高度,一般不應低于3.2m;
⑤室內放置的容器有可能形成燃燒爆炸氣體時,電氣裝置應達到防爆要求,容器要可靠地接地;存放有毒氣體容器的屋內,要有通風裝置;有些特殊場所還要考慮萬一發生介質滲漏的中和處理設施。
⑥對安放高壓和超高壓容器的房屋還應做到:用防火墻把它與生產廠房隔開;盡可能有采有輕質屋頂;同時裝有幾臺容器的房屋,要根據容器容量將容器分別安設在用防火墻隔開的單間內,每臺容器應有單獨的基礎,并且不要與墻柱及其他裝備的基礎相連。
(2)壓力容器的合理使用
①操作人員必須嚴格執行容器安全操作規程。其操作規程應包括如下內容:1)要規定操作工藝指標,如最高工作壓力,最高、最低工作溫度等;2)規定操作方法,如開停車操作程序及注意事項等;3)應標明容器運行中的重點檢查部位與項目,并說明容器在運行中可能出現的異常現象與處理方法;4)應標明間歇生產容器停用時檢查的部位與項目;5)應規定定時、定點進行巡回檢查的內容等。
②建立崗位責任制。操作人員應經過培訓考試合格,才能上崗操作。操作人員必須熟悉本崗位壓力容器的技術性能、結構原理、工藝指標以及可能發生事故和應采取的措施,熟悉工藝流程和管線上閥門及盲板的位置,避免發生誤操作。
③加強巡回檢查。應認真進行對安全閥、壓力表及防爆膜等安全附件的巡回檢查。
④應嚴格控制工藝參數,嚴禁超壓超溫運行,如容器承受壓力或溫度超過最高允許壓力或溫度時,應立即按操作規程規定的程序,采取緊急措施。
⑤容器在加載時,速度不宜過快。應盡量避兔操作中頻繁地大幅度的壓力波動,力求平穩操作。
⑥盡量減少容器的開停次數。
(3)壓力容器的維護
①采取有效措施,防止大氣與介質對容器的腐蝕(如噴涂、電涂、涂層、襯里等),并經常檢查,保證完好。
②容器上的安全裝置(安全閥、卸壓孔、壓力表及防爆膜等)應保持清潔、完好、靈敏、準確、可靠、并定期進行檢查和校驗。
③采取有效的措施,防止容器和有關連接管道的“跑、冒、滴、漏”,一有問題,應立即消除。
④經常檢查容器上緊固件,力求保持齊全、完整、緊固、可靠。
⑤發現有振動、摩擦現象,應及時采取措施排除或減輕。
⑥檢查容器的靜電接地情況,保證接地裝置完整、良好。
⑦保持絕熱層及保溫層完好。
⑧停用、封存的容器也應定期進行維護。
(4)壓力容器的檢修
壓力容器的檢修應符合國家勞動部及有關部門的規定,嚴格按周期有計劃地進行檢驗與檢修,在進行檢驗與檢修時應注意以下幾點:
①容器內部有壓力時,不得對任何受壓元件進行任何修理或緊固作業。
②泄壓、降溫要按操作程序進行。只有在掃線置換中和合格,發給并交出動火證后,才能進行檢修工作。要切斷一切與之連接的汽源與物料道路,尤其是易燃有毒氣體的物料,必要時加設盲板嚴密封閉,以防閥門泄漏,造成事故。
③檢修人員在進入容器檢驗或檢修時,要有專人監護,并有聯絡信號。檢驗結束,要指定專人消除容器內的雜物,并及時進行封密(較大容器要有封塔封罐證)。
④容器修理或改造后,必須保證受壓元件的原有強度和制造質量。在進行修補、開孔、更換筒體、焊接或熱處理時,必須預先提出方案,經過校核驗算,按技術規范和制造工藝要求提出正確的焊接工藝方法。經使單位主管容器技術人員同意,二、三類容器還應經本單位技術總負責人批準,三類容器還須報主管部門及同級勞動部門備案后,才能動工。
⑤容器如由本單位自行檢修時,應派考試合格技術較好的焊工進行。如委托外單位施工,必須是經批準的施工單位并持有合格證的焊工才能進行修理。焊縫的質量十分重要,必須予以保證。
⑥不得在壓力容器上任意開孔或加工改裝。
⑦檢修后要進行必要的檢驗和試驗。
4)壓力容器的定期檢驗
(1)定期檢驗的意義
壓力容器在經過長期運行后,會產生下列情況:
①長期頻繁地加壓減壓,或大幅度地壓力波動,使材料中有缺陷的地方或應力集中的部位,會產生疲勞裂紋;
②由于設計不合理,如強度不夠,應力大;,或操作不當,超載運行等原因,使材料產生塑性變形;
③容器內的工作介質,很多是有腐蝕性的,材料受到各種腐蝕,使壁厚減薄(局部或均勻減薄),甚至導致材料的物理性能變化、機械性能下降,以致不能承受規定的工作壓力;
④制成的容器可能由于材質或制造過程中的微小缺陷而在產品檢驗中未能發現,但會在使用中逐漸擴大;
⑤長期處于高溫高壓下工作,使材料產生蠕變;
⑥由于結構材料焊接工藝不當或焊接質量低劣,造成焊縫附近的材料應力過大或晶格變粗,因而產生裂紋。
定期檢驗是在壓力容器使用過程中,根據它的使用條件,每隔一定期限對它進行一次全面的技術檢查,包括必要的試驗,以便及早發現缺陷,采取措施,防止重大事故發生。
(2)定期檢驗的周期
壓力容器的定期檢驗一般可分為外部檢查、內外部檢驗和全面檢驗三種。檢驗是在容器停用期中進行的,其周期應根據容器的技術狀況、使用條件和有關規定由使用單位結合具體情況自行確定。但每年至少進行一次外部檢查,每三年至少進行一次內外部檢驗,每六年至少進行一次全面檢驗。
遇到下列情況時,定期檢驗間隔期應縮短:
①裝有強烈腐蝕介質和運行中發現有嚴重缺陷時,每年至少進行一次內部檢驗;
②無法進行內部檢驗時,每三年進行一次耐壓試驗;
③使用期達15年后,每二年至少進行—次內外部檢驗;使用期達20年后,每年至少進行一次內外部檢驗,并據以確定全面檢驗的時間或能否繼續使用;
④介質對容器材料的腐蝕情況不明,材料焊接性能差或制造時曾多次產生裂紋者,一般要求投產使用一年就應立即進行內部檢驗。對外部有保溫層的壓力容器進行全面檢驗時,應根據缺陷情況拆除保溫層。
(3)外部檢查內容
外部檢查內容有:
①容器外表面有無腐蝕現象,銘牌是否完好;
②容器本體、接口部位、受壓元件、焊接接頭等有無裂紋、過熱、變形、泄漏等不正常現象;
③容器的保溫層、防腐層有否破損、脫落、潮濕、跑冷現象;
④檢漏孔、信號孔有無漏液、漏氣;檢漏管是否暢通;
⑤與壓力容器相鄰的管道和構件有無異常振動、響聲及互相摩擦現象;
⑥安全附件是否齊全、靈敏、可靠;
⑦緊固螺栓是否完好;基礎有無下沉、傾斜、開裂;支承及支座有否損壞;
⑧排放(疏水、排污)裝置是否暢通正常。
(4)內外部檢驗內容
內外部檢驗內容包括:
①外部檢查的全部內容;
②進行結構檢驗。應重點檢驗下列各部位是否完好:筒體與封頭的連接;方型孔、人孔、檢查孔及其補強;角接、搭接以及布置不合理的焊縫;封頭(端蓋);支座及支承;法蘭盤;排污口。
③所有焊縫、封頭過渡區或其它應力集中部位有無斷裂或裂紋。對有懷疑的部位,應進行表面檢查,如發現裂紋,應采用超聲波或射線進一步抽查,抽查長度不小于焊縫總長的20%。
④有襯里的容器,其襯里是否有凸起、開裂及其他損壞現象,如發現襯里有上述缺陷而可能影響容器本體時,應將該處襯里部分或全部拆除,并檢查容器殼體是否有腐蝕或裂紋。
⑤通過檢查,如發現容器內外表面有腐蝕等現象時,應對懷疑部位進行多處壁厚測定,測得的壁厚如小于所規定的最小壁厚時,應重新進行強度核算,并提出可否繼續使用的意見和許用工作壓力。
⑥容器內壁因受溫度、壓力、介質腐蝕作用,懷疑金屬材料的金相組織有可能破壞時(如脫炭、應力腐蝕、晶間腐蝕、疲勞裂紋等),就應進行金相檢驗和表面硬度測定,并做出檢驗報告。
⑦對高壓、超高壓容器的主要緊固螺栓應逐個進行外形檢查(螺紋、圓角過渡部位、長度等),并用磁粉或著色探傷檢查有無裂紋。
(5)全面檢驗內容
全面檢驗內容包括:
①包括上述外部檢查和內外部檢驗的全部內容。
②對主要焊縫進行無損探傷抽查,抽查長度不小于該焊縫長度的20%。對高壓、超高壓的反應容器,應進行100%超聲波探傷,必要時還需表面探傷。
③對設計壓力<0.29MPa、且Pw•V<490MPa•l,其工作介質為非易燃或無毒的容器,如采用10倍以上放大鏡檢查或表面探傷,沒有發現缺陷時,可不作射線或超聲波探傷抽查。
④容器內外部檢驗合格后,按規定進行耐壓試驗。
(6)定期檢驗的方法
壓力容器的定期撿驗可分為破壞性檢驗和非破壞性檢驗兩大類,采用何種方法要根據生產情況、技術要求和有關標準確定。
(7)耐壓試驗和氣密性試驗
①耐壓試驗
耐壓試驗是指壓力容器停機檢驗時,所進行的超過最高工作壓力的液壓試驗。
有下列情況之一的壓力容器。內外部檢驗合格后必須進行耐壓試驗。
a用焊接方法修理或更換主要受壓元件的;
b改變使用條件且超過原設計參數的;
c更換襯里在重新換上襯里前;
d停止使用兩年重新啟用的;
e新安裝的或移裝的;
f無法進行內部檢驗的;
g使用單位對壓力容器的安全性能有懷疑的。
②氣密性試驗
有的容器不能進行水壓試驗,一般由氣密試驗代替。如:容積特大的容器;容器基礎不能承受容器充水后的總重量;不宜充水的容器(如隔熱層襯里容器等)。
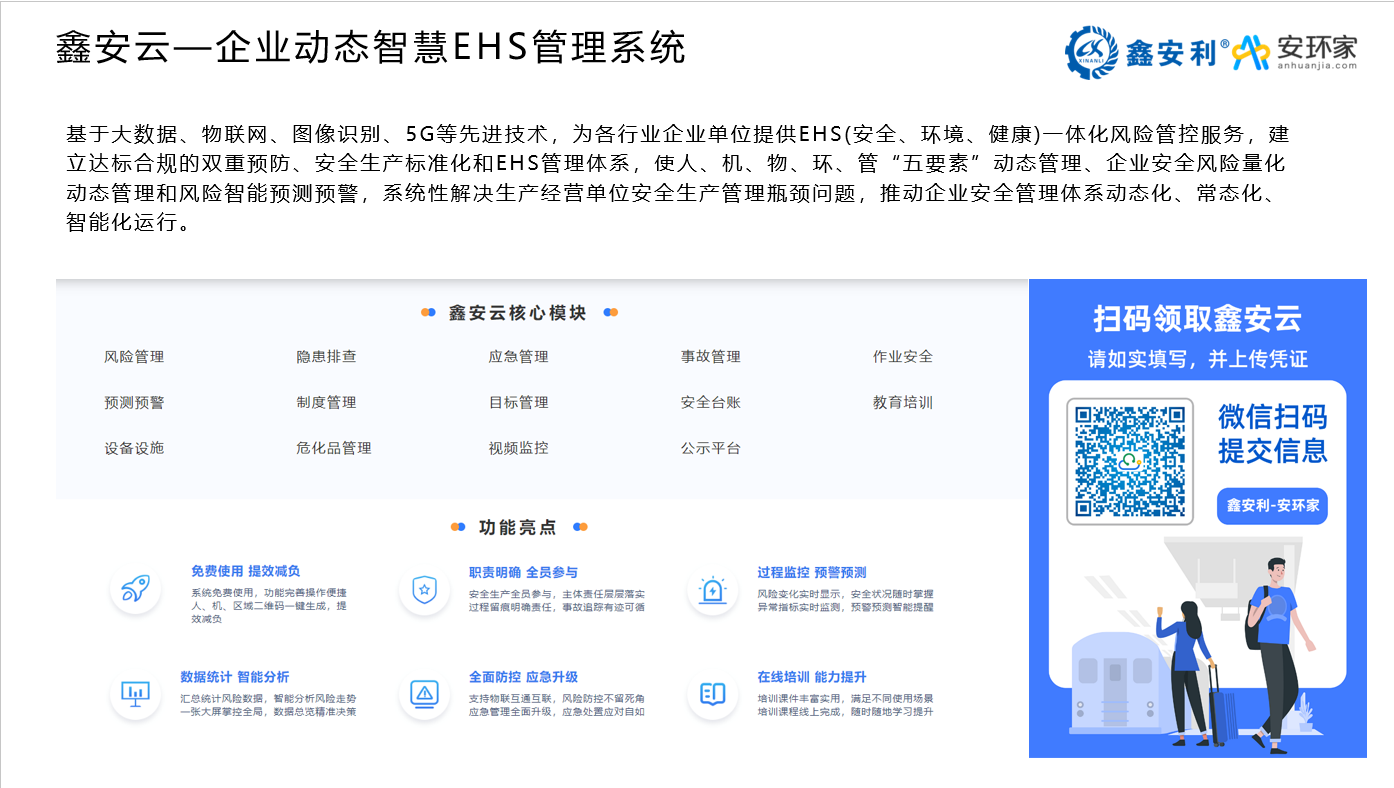