一、機械設備的危害因素
一、機械的危害
1.靜止的危險
設備處于靜止狀態時存在的危險即當人接觸或與靜止設備作相對運動時可引起的危險。包括:
(l)切削刀具有刀刃。
(2)機械設備突出的較長的部分,如設備表面上的螺栓、吊鉤、手柄等。
(3)毛坯、工具、設備邊緣鋒利和粗糙表面,如未打磨的毛刺、銳角、翹起的銘牌等。
(4)引起滑跌的工作平臺,尤其是平臺有水或油時更為危險。
2.直線運動的危險
指作直線運動的機械所引起的危險,又可分接近式的危險和經過式的危險。
(l)接近式的危險:這種機械進行往復的直線運動,當人處在機械直線運動的正前方而未及時躲讓時將受到運動機械的撞擊或擠壓。
①縱向運動的構件,如龍門刨床的工作臺、牛頭刨床的滑枕、外國磨床的往復工作臺等。
②橫向運動的構件,如升降式銑床的工作臺。
(2)經過式的危險指人體經過運動的部件引起的危險。包括:
①單純作直線運動的部位,如運轉中的帶鍵、沖模。
②作直線運動的凸起部分,如運動時的金屬接頭。
③運動部位和靜止部位的組合,如工作臺與底座組合,壓力機的滑塊與模具。
④作直線運動的刃物,如牛頭刨床的刨刀、帶鋸床的帶鋸。
3.機械旋轉運動的危險
指人體或衣服被卷進旋轉機械部位引起的危險。
(l)卷進單獨旋轉運動機械部件中的危險,如主軸、卡盤、進給絲杠等單獨旋轉的機械部件以及磨削砂輪、各種切削刀具,如銑刀、鋸片等加工刃具。
(2)卷進旋轉運動中兩個機械部件間的危險,如朝相反方向旋轉的兩個軋輥之間,相互嚙合的齒輪。
(3)卷進旋轉機械部件與固定構件間的危險,如砂輪與砂輪支架之間,有輻條的手輪與機身之間。
(4)卷進旋轉機械部件與直線運動部件間的危險,如皮帶與皮帶輪、鏈條與鏈輪、齒條與齒輪、滑輪與繩索間、卷場機絞筒與絞盤等。
(5)旋轉運動加工件打擊或絞軋的危險,如伸出機床的細長加工件。
(6)旋轉運動件上凸出物的打擊、如皮帶上的金屬皮帶扣、轉軸上的鍵、定位螺絲、聯軸器螺絲等。
(7)孔洞部分有些旋轉零部件,由于有孔洞部分而具有更大的危險性。如風扇、葉片,帶幅條的滑輪、齒輪和飛輪等。
(8)旋轉運動和直線運動引起的復合運動,如凸輪傳動機構、連桿和曲軸。
4.機械飛出物擊傷的危險
(l)飛出的刀具或機械部件,如未夾緊的刀片、緊固不牢的接頭、破碎的砂輪片等。
(2)飛出的切屑或工件,如連續排出或破碎而飛散的切屑、鍛造加工中飛出的工件。
二、非機械的危害
1.電擊傷
指采用電氣設備作為動力的機械以及機械本身在加工過程中產生的靜電引起的危險。
(l)靜電危險如在機械加工過程中產生的有害靜電,將引起爆炸、電擊傷害事故。
(2)觸電危險如機械電氣設備絕緣不良,錯誤地接線或誤操作等原因造成的觸電事故。
2.灼燙和冷危害
如在熱加工作業中被高溫金屬體和加工件灼燙的危險,或與設備的高溫表面接觸時被灼燙的危險,在深冷處理或與低溫金屬表面接觸時被凍傷的危險。
3.振動危害
在機械加工過程中使用振動工具或機械本身產生的振動所引起的危害,按振動作用于人體的方式,可分為局部振動和全身振動。
(l)全身振動。由振動源通過身體的支持部分將振動傳布全身而引起的振動危害。
(2)局部振動。如在以手接觸振動工具的方式進行機械加工時,振動通過振動工具、振動機械或振動工件傳向操作者的手和臂,從而給操作者造成振動危害。
4.噪聲危害
機械加工過程或機械運轉過程所產生的噪聲而引起的危害。
機械引起的噪聲包括:
(l)機械性噪聲。由于機械的撞擊、摩擦、轉動而產生的噪聲,如球磨機、電鋸、切削機床在加工過程中發出的噪聲。
(2)電磁性噪聲。由于電機中交變力相互作用而發生的噪聲,如電動機、變壓器等在運轉過程中發出的噪聲。
(3)流體動力性噪聲。由于氣體壓力突變或流體流動而產生的噪聲、如液壓機械、氣壓機械設備等在運轉過程中發出的噪聲。
5.電離輻射危害
指設備內放射性物質、x射線裝置、r射線裝置等超出國家標準允許劑量的電離輻射危害。
6.非電離輻射危害
非電離輻射是指紫外線、可見光、紅外線、激光和射頻輻射等,當超出衛生標準規定劑量時引起的危害。如從高頻加熱裝置中產生的高頻電磁波或激光加工設備中產生的強激光等非電磁輻射危害。
7.化學物危害
機械設備在加工過程中使用或產生的各種化學物所引起的危害。包括:
(l)易燃易爆物質的灼傷、火災和爆炸危險。
(2)工業毒物的危害是指機械加工設備在加工過程中使用或產生的各種有毒物質引起的危害。工業毒物可能是原料、輔助材料、半成品、成品、也可能是副產品、廢棄物、夾雜物,或其中含有毒成分的其他物質。
(3)酸、堿等化學物質的腐蝕性危害,如在金屬的清洗和表面處理時產生的腐蝕性危害。
8.粉塵危害
指機械設備在生產過程中產生的各種粉塵引起的危害。粉塵來源包括:
(l)某些物質加熱時產生的蒸汽在空氣中凝結或被氧化所形成的粉塵,如熔煉黃銅時,鋅蒸汽在空氣中冷凝、氧化形成氧化鋅煙塵。
(2)固體物質的機械加工或粉碎,如金屬的拋光、石墨電極的加工。
(3)鑄造加工中,清砂時或在生產中使用的粉末狀物質,在混合、過篩、包裝、搬運等操作時產生的以及沉積的粉塵,由于振動或氣流的影響再次浮游于空氣中的粉塵(二次揚塵)。
(4)有機物的不完全燃燒,如木材、焦油、煤炭等燃燒時所產生的煙。
(5)焊接作業中,由于焊藥分解,金屬蒸發所形成的煙塵。
9.生產環境,指異常的生產環境
(l)照明
工作區照度不足,照度均度不夠,亮度分布不當,光或色的對比度不當,以及存在頻閃效應、眩光效應。
(2)氣溫
工作區溫度過高、過低或急劇變化。
(3)氣流
工作區氣流速度過大、過小或急劇變化。
(4)濕度
工作區濕度過大或過小。
二、機械事故發生的直接、間接原因
一、機械事故發生的直接原因
1.機械的不安全狀態
(l)防護、保險、信號等裝置缺乏或有缺陷。
①無防護
無防護罩,無安全保險裝置,無報警裝置,無安全標志,無護欄或護欄損壞,設備電氣未接地,絕緣不良,噪聲大,無限位裝置等。
②防護不當
防護罩未在適當位置,防護裝置調整不當,安全距離不夠,電氣裝置帶電部分裸露等。
(2)設備、設施、工具、附件有缺陷。
①設備在非正常狀態下運行,設備帶“病”運轉,超負荷定轉等。
②維修、調整不良,設備失修,保養不當,設備失靈,未加潤滑油等。
③機械強度不夠,絕緣強度不夠,起吊重物的繩索不合安全要求等。
④設計不當,結構不合安全要求,制動裝置有缺陷,安全間距不夠,工件上有鋒利毛刺、毛邊、設備上有鋒利倒棱等。
(3)個人防護用品、用具。如防護服、手套、護目鏡及面罩、呼吸器官護具、安全帶、安全帽、安全鞋等缺少或有缺陷。
①所用防護用品、用具不符合安全要求。
②無個人防護用品、用具。
(4)生產場地環境不良
①通風不良
無通風,通風系統效率低等。
②照明光線不良
包括照度不足,作業場所煙霧煙塵彌漫、視物不清,光線過強,有眩光等。
③作業場地雜亂
工具、制品、材料堆放不安全。
④作業場所狹窄。
(5)操作工序設計或配置不安全,交叉作業過多。
(6)地面滑,地面有油或其他液體,有冰雪。地面有易滑物如圓柱形管子、料頭、滾珠等。
(7)交通線路的配置不安全。
(8)貯存方法不安全,堆放過高、不穩。
2.操作者的不安全行為
這些不安全行為可能是有意的或無意的。
(l)操作錯誤、忽視安全、忽視警告包括未經許可開動、關停、移動機器;開動、關停機器時未給信號;開關未鎖緊,造成意外轉動;忘記關閉設備;忽視警告標志、警告信號,操作錯誤(如按錯按鈕、閥門、搬手、把柄的操作方向相反);供料或送料速度過快,機械超速運轉;沖壓機作業時手伸進沖模;違章駕駛機動車;工件刀具緊固不牢.,用壓縮空氣吹鐵屑等。
(2)使用不安全設備。臨時使用不牢固的設施如工作梯,使用無安全裝置的設備,臨時拉線不符合安全要求等。
(3)機械運轉時加油、修理、檢查、調整、焊接或清掃。
(4)造成安全裝置失效。拆除了安全裝置,安全裝置失去作用。
調整錯誤造成安全裝置失效。
(5)用手代替工具操作。用手代替手動工具,用手清理切屑。不用夾具固定,用手拿工件進行機械加工等。
(6)攀、坐危險位置(如平臺護欄、吊車吊鉤等)。
(7)物體(成品、半成品、材料、工具、切屑和生產用品等)存放不當。
(8)穿不安全裝束如在有旋轉零部件的設備旁作業時穿著過于肥大、寬松的服裝、操縱帶有旋轉零部件的設備時戴手套,穿高跟鞋、涼鞋或拖鞋進入車間等。
(9)必須使用個人防護用品,用具的作業或場合中,忽視其使用,如未戴各種個人防護用品。
(10)無意或為排除故障而靠近危險部位,如在無防護罩的兩個相對運動零部件之間清理卡住物時,可能造成擠傷、夾斷、切斷、壓碎或人的肢體被卷進而造成嚴重的傷害。
二、間接原因
幾乎所有事故的間接原因都與人的錯誤有關,盡管與事故直接有關的操作人員并沒有出錯。這些間接原因可能是由于設計人員、設備制造、安裝調試、維護保養等人所犯的錯誤。間接原因包括:
1.技術和設計上的缺陷
工業構件、建筑物(如室內照明、通風)、機械設備、儀器儀表、工藝過程、操作方法、維修檢驗等的設計和材料使用等方面存在的問題。
(l)設計錯誤包括強度計算不準,材料選用不當,設備外觀不安全,結構設計不合理,操縱機構不當,未設計安全裝置等。即使設計人員選用的操縱器是正確的,如果在控制板上配置的位置不當,也可能使操作人員混淆而發生操作錯誤,或不適當地增加了操作人員的反應時間而忙中出錯。
設計人員還應注意作業環境設計,不適當的操作位置和勞動姿勢都可能引起操作人員疲勞或思想緊張而容易出錯。
(2)制造錯誤
即使設計是正確的,如果制造設備時發生錯誤,也會成為事故隱患。在生產關鍵性部件和組裝時,應特別注意防止發生錯誤。常見的制造錯誤有加工方法不當(如用鉚接代替焊接),加工精度不夠,裝配不當,裝錯或漏裝了零件,零件未固定或固定不牢。工件上的劃痕、壓痕、工具造成的傷痕以及加工粗糙可能造成用力集中而使設備在運行時出現故障。
(3)安裝錯誤
安裝時旋轉零件不同軸,軸與軸承、齒輪嚙合調整不好,過緊過松,設備不水平。地腳螺擰緊,設備內遺留工具、零件、棉紗等,都可能使設備發生故障。
(4)維修錯誤
沒有定時對運動部件加潤滑油,在發現零部件出現惡化現象時沒有按維修要求更換零部件,都是維修錯誤。當設備大修重新組裝時,可能會發生與新設備最初組裝時發生的類似錯誤。安全裝置是維修人員檢修的重點之一。安全裝置失效而未及時修理,設備超負荷運行而未制止,設備帶“病”運轉,都屬于維修不良。
2.管理缺陷
(l)無安全操作規程或安全規程不完善。
(2)規章制度執行不嚴,有章不循。
(3)對現場工作缺乏檢查或指導錯誤。
(4)勞動制度不合理
(5)缺乏監督。
3.教育培訓不夠,未經培訓上崗,操作者業務素質低,缺乏安全知識和自我保護能力,不懂安全操作技術,操作技能不熟練,工作時注意力不集中,工作態度不負責。受外界影響而情緒波動,不遵守操作規程,都是事故的間接原因。
4.對安全工作不重視,組織機構不健全,沒有建立或落實現代安全生產責任制。沒有或不認真實施事故防范措施,對事故隱患調查整改不力。關鍵是企業領導不重視。
三、機械設備的防范措施
一、危險性大的設備
根據事故統計。我國規定危險性比較大、事故率比較高的設備有:壓力機、沖床、剪床、壓正機、壓印機、木工刨床、木工鋸床、木工造型機、塑料注射成型機、煉膠機、壓磚機、農用脫料機、紙頁壓光機、起重設備、鍋爐、壓力容器、電氣設備等。
這些設備在出廠前必須配備好安全防護裝置。
二、機械的危險部位
操作人員易于接近的各種可動零、部件都是機械的危險部位,機械加工設備的加工區也是危險部位。
常見的危險零部位件有:
1.旋轉軸。
2.相對傳動部件如嚙合的明齒輪。
3.不連續的旋轉零件,如風機葉片,成對帶齒滾筒。
4.皮帶與皮帶輪,鏈與鏈輪。
5.旋轉的砂輪。
6.活動板和固定板之間靠近時的壓板。
7.往復式沖壓工具如沖頭和模具。
8.帶狀切割工具如帶鋸。
9.蝸輪和蝸桿。
10.高速旋轉運動部件的表面如離心機轉鼓。
11.聯接桿與鏈環之間的夾子。
12.旋轉的刀具刃具。
13.旋轉的曲軸和曲柄。
14.旋轉運動部件的凸出物,如鍵、定位螺絲。
15.旋轉的攪拌機、攪拌翅。
16.帶尖角、銳邊或利棱的零部件。
17.鋒利的工具。
18.帶有危險表面的旋轉圓筒如脫粒機。
19.運動皮帶上的金屬接頭(皮帶扣)。
20.飛輪。
21.聯軸節上的固定螺絲。
22.過熱過冷的表面。
23.電動工具的把柄。
24.設備表面上的毛刺、尖角、利棱、凹凸。
25.機械加工設備的工作區。
三、危險的作業
本身具有較大的危險性的作業稱為特種作業、其危險性和事故率比一般作業大。包括:
1.電工作業。
2.壓力容器操作。
3.鍋爐司爐。
4.高溫作業。
5.低溫作業。
6.粉塵作業。
7.金屬焊接氣割作業。
8,起重機械作業。
9.機動車輛駕駛。
10.高處作業等。
特種作業人員必須經過現代安全技術培訓、考核合格后才能上崗操作。
四、機械傷害形式
機械傷害的形式可分為8類:
l.咬入和擠壓
這種傷害是在兩個零部件之間產生的,其中一個或兩個是運動零部件,這時人體的四肢被卷進兩個部件的接觸處。
(l)擠壓
這種危險不一定兩個部件完全接觸,只要距離很近,四肢就可能受擠壓。除直線運動部件外,人手還可能在螺旋輸送機、塑料注射成型機中受擠壓。如果安裝距離過近或操作不當,如在轉動閥門的平輪或關閉防護罩時也會受擠壓。
(2)咬入(咬合)
典型的咬入點(也可叫擠壓點)是嚙合的明齒輪、皮帶與皮帶輪、鏈與鏈輪,兩個相反方向轉動的軋輥。一般是兩個運動部件直接接觸,將人的四肢卷進運轉中的咬人點。
2.碰撞和撞擊
這種傷害有兩種主要形式,一種是比較重的往復運動部件撞人,傷害程度與運動部件的質量和運動速度的乘積即部件的動量有關。另一種是飛來物及落下物的撞擊造成的傷害。飛來物主要指高速旋轉的零部件、工具、工件、緊固件固定不牢或松脫時,會以高速甩出。雖然這些物體質量很大,但轉速很高,而動能與速度的平方成正比,即動能很大。飛來物撞擊人體,能使人造成嚴重的傷害。高速飛出的切屑也能使人受到傷害。
3.接觸
當人體接觸機械的運動部件或運動部件直接接觸人體時都可能造成機械傷害。運動部件一般指具有銳邊、尖角、利棱的刀具,有凸出物的表面和摩擦表面;也包括過熱、過冷表面和電絕緣不良而導電的靜止物體的表面。后者不屬于機械傷害。接觸傷害有4類:
(l)夾斷
當人體伸入兩個接觸部件中間時,人的肢體可能被夾斷。夾斷與擠壓不同,夾斷發生在兩個部件的直接接觸,擠壓不一定完全接觸,兩個部件不一定是刀刃。其中一個是運動部件或兩個都是運動部件都能造成夾斷傷害。
(2)剪切
兩個具有銳利邊刃的部件,在一個或兩個部件運動時,能產生剪刀作用。當兩者靠近而人的四肢伸入時,刀刃能將四肢切斷。
(3)割傷和擦傷
這種傷害可以發生在運動機械和靜止設備上。當靜止設備上有尖角和銳邊,而人體與該設備作相對運動時,能被尖角和銳邊割傷。當然有尖角、銳邊的部件轉動時,對人造成的傷害更大,如人體接觸旋轉刀具、鋸片,都會造成嚴重的割傷。高速旋轉的粗糙面如砂輪能使人擦傷。
(4)卡住或纏住
具有卡住作用的部位是指靜止設備表面或運動部件上的尖角或凸出物。這些凸出物能絆住、纏住人寬松的衣服,甚至皮膚。當卡住后,有引向另一種危險,特別是運動部件上的凸出物、皮帶接頭、車床的轉軸、加工件都能將人的手套、衣袖、頭發、辮子甚至工作服口袋中擦機器用的綿紗纏住而使人造成嚴重傷害。
五、機械傷害的結果
機械傷害的后果一般比較嚴重,輕則損傷皮肉,重則斷肢致殘,甚至危及生命。GB6441—86((企業職工傷亡事故分類》對傷害后果有明確的規定。
GB6441—86規定以損失工作日來劃分傷害程度。損失工作日是指被傷害者失能的工作時問。
該規定對計算方法有嚴格的標準,計算損失工作日后即可確定傷害程度。其分類如下:
①輕傷
輕傷是指損失工作日為105—7天的失能傷害。
②重傷
重傷是指相當于現定損失工作日等于或超過105日的失能傷害。
③死亡
四、機械設備本質安全措施
一、本質安全的目的
本質安全化的目的是:運用現代科學技術,特別是安全科學的成就,從根本上消除能形成事故的主要條件;如果暫時達不到時,則采取兩種或兩種以上的相對安全措施,形成最佳組合的安全體系,達到最大限度的安全。同時盡可能采取完善的防護措施,增強人體對各種危害的抵抗能力。
二、本質安全化的內容
設備的本質安全措施可以通過設備本身和控制器的安全設計來實現。
l.本質安全化的基本思路
(l)從根本上消除發生事故的條件。許多機械事故是由于人體接觸了危險點、如果將危險操作采用自動控制、用專用工具代替人手操作,實現機械化等都是保證人身安全的有效措施。
(2)設備能自動防止操作失誤和設備故障。設備應有自動防范措施,以避免發生事故。這些措施應能達到:即使操作失誤,也不會導致設備發生事故.即使出現故障,應能自動排除,切換或安全停機;當設備發生故障時,不論操作人員是否發現,設備應能自動報警,并作出應急反應,更理想的是還能顯示設備發生故障的部位。
2.常用的措施
(l)采用機械化、自動化和遙控技術。
(2)采用可靠性設計,提高機械設備的可靠性。詳見下一節。
(3)采用安全防護裝置。當無法消除危險因素時,采用安全防護裝置隔離危險因素是最常用的技術措施。
(4)安裝保險裝置。保險裝置又叫故障保險裝置。這種裝置的作用與安全防護裝置稍有不同。它能在設備產生超壓、超溫、超速、超載、超位等危險因素時,進行自動控制并消除或減弱上述危險。安全閥、單向閥、超載保護裝置、限速器、限位開關、爆破片、熔斷器、保險絲、力短限制器、極限位置限制器等都是常用的保險裝置。
(5)采用自監測、報警和處理系統。利用現代化儀器儀表對運行中的設備狀態參數進行在線監測和故障診斷。
(6)采用冗余技術。冗余技術是可靠性設計常采用的一種技術,即在設計中增加冗余元件或冗余(備用)設備,平時只用其中一個,當發生事故時,冗余設備或冗余元件能自動切換。
(7)采用傳感技術。在危險區設置光電式、感應式、壓力傳感式傳感器,當人進入危險區,可立即停機,終止危險運動。
(8)安裝緊急停車開關。
(9)向操作者提供機械關鍵安全功能是否正常(設備的自檢功能)的信息。
(10)設計程序聯鎖開關。設計對出現錯誤指令時,禁止啟動的操縱器。這些關鍵程序只有在正常操作指令下才能啟動機械。
(ll)配備使操作者容易觀察的、能顯示設備運行狀態和故障的顯示器。
(12)采用多重安全保障措施。對于危險性大的作業,要求設備運行絕對安全可靠。
一、機械的危害
1.靜止的危險
設備處于靜止狀態時存在的危險即當人接觸或與靜止設備作相對運動時可引起的危險。包括:
(l)切削刀具有刀刃。
(2)機械設備突出的較長的部分,如設備表面上的螺栓、吊鉤、手柄等。
(3)毛坯、工具、設備邊緣鋒利和粗糙表面,如未打磨的毛刺、銳角、翹起的銘牌等。
(4)引起滑跌的工作平臺,尤其是平臺有水或油時更為危險。
2.直線運動的危險
指作直線運動的機械所引起的危險,又可分接近式的危險和經過式的危險。
(l)接近式的危險:這種機械進行往復的直線運動,當人處在機械直線運動的正前方而未及時躲讓時將受到運動機械的撞擊或擠壓。
①縱向運動的構件,如龍門刨床的工作臺、牛頭刨床的滑枕、外國磨床的往復工作臺等。
②橫向運動的構件,如升降式銑床的工作臺。
(2)經過式的危險指人體經過運動的部件引起的危險。包括:
①單純作直線運動的部位,如運轉中的帶鍵、沖模。
②作直線運動的凸起部分,如運動時的金屬接頭。
③運動部位和靜止部位的組合,如工作臺與底座組合,壓力機的滑塊與模具。
④作直線運動的刃物,如牛頭刨床的刨刀、帶鋸床的帶鋸。
3.機械旋轉運動的危險
指人體或衣服被卷進旋轉機械部位引起的危險。
(l)卷進單獨旋轉運動機械部件中的危險,如主軸、卡盤、進給絲杠等單獨旋轉的機械部件以及磨削砂輪、各種切削刀具,如銑刀、鋸片等加工刃具。
(2)卷進旋轉運動中兩個機械部件間的危險,如朝相反方向旋轉的兩個軋輥之間,相互嚙合的齒輪。
(3)卷進旋轉機械部件與固定構件間的危險,如砂輪與砂輪支架之間,有輻條的手輪與機身之間。
(4)卷進旋轉機械部件與直線運動部件間的危險,如皮帶與皮帶輪、鏈條與鏈輪、齒條與齒輪、滑輪與繩索間、卷場機絞筒與絞盤等。
(5)旋轉運動加工件打擊或絞軋的危險,如伸出機床的細長加工件。
(6)旋轉運動件上凸出物的打擊、如皮帶上的金屬皮帶扣、轉軸上的鍵、定位螺絲、聯軸器螺絲等。
(7)孔洞部分有些旋轉零部件,由于有孔洞部分而具有更大的危險性。如風扇、葉片,帶幅條的滑輪、齒輪和飛輪等。
(8)旋轉運動和直線運動引起的復合運動,如凸輪傳動機構、連桿和曲軸。
4.機械飛出物擊傷的危險
(l)飛出的刀具或機械部件,如未夾緊的刀片、緊固不牢的接頭、破碎的砂輪片等。
(2)飛出的切屑或工件,如連續排出或破碎而飛散的切屑、鍛造加工中飛出的工件。
二、非機械的危害
1.電擊傷
指采用電氣設備作為動力的機械以及機械本身在加工過程中產生的靜電引起的危險。
(l)靜電危險如在機械加工過程中產生的有害靜電,將引起爆炸、電擊傷害事故。
(2)觸電危險如機械電氣設備絕緣不良,錯誤地接線或誤操作等原因造成的觸電事故。
2.灼燙和冷危害
如在熱加工作業中被高溫金屬體和加工件灼燙的危險,或與設備的高溫表面接觸時被灼燙的危險,在深冷處理或與低溫金屬表面接觸時被凍傷的危險。
3.振動危害
在機械加工過程中使用振動工具或機械本身產生的振動所引起的危害,按振動作用于人體的方式,可分為局部振動和全身振動。
(l)全身振動。由振動源通過身體的支持部分將振動傳布全身而引起的振動危害。
(2)局部振動。如在以手接觸振動工具的方式進行機械加工時,振動通過振動工具、振動機械或振動工件傳向操作者的手和臂,從而給操作者造成振動危害。
4.噪聲危害
機械加工過程或機械運轉過程所產生的噪聲而引起的危害。
機械引起的噪聲包括:
(l)機械性噪聲。由于機械的撞擊、摩擦、轉動而產生的噪聲,如球磨機、電鋸、切削機床在加工過程中發出的噪聲。
(2)電磁性噪聲。由于電機中交變力相互作用而發生的噪聲,如電動機、變壓器等在運轉過程中發出的噪聲。
(3)流體動力性噪聲。由于氣體壓力突變或流體流動而產生的噪聲、如液壓機械、氣壓機械設備等在運轉過程中發出的噪聲。
5.電離輻射危害
指設備內放射性物質、x射線裝置、r射線裝置等超出國家標準允許劑量的電離輻射危害。
6.非電離輻射危害
非電離輻射是指紫外線、可見光、紅外線、激光和射頻輻射等,當超出衛生標準規定劑量時引起的危害。如從高頻加熱裝置中產生的高頻電磁波或激光加工設備中產生的強激光等非電磁輻射危害。
7.化學物危害
機械設備在加工過程中使用或產生的各種化學物所引起的危害。包括:
(l)易燃易爆物質的灼傷、火災和爆炸危險。
(2)工業毒物的危害是指機械加工設備在加工過程中使用或產生的各種有毒物質引起的危害。工業毒物可能是原料、輔助材料、半成品、成品、也可能是副產品、廢棄物、夾雜物,或其中含有毒成分的其他物質。
(3)酸、堿等化學物質的腐蝕性危害,如在金屬的清洗和表面處理時產生的腐蝕性危害。
8.粉塵危害
指機械設備在生產過程中產生的各種粉塵引起的危害。粉塵來源包括:
(l)某些物質加熱時產生的蒸汽在空氣中凝結或被氧化所形成的粉塵,如熔煉黃銅時,鋅蒸汽在空氣中冷凝、氧化形成氧化鋅煙塵。
(2)固體物質的機械加工或粉碎,如金屬的拋光、石墨電極的加工。
(3)鑄造加工中,清砂時或在生產中使用的粉末狀物質,在混合、過篩、包裝、搬運等操作時產生的以及沉積的粉塵,由于振動或氣流的影響再次浮游于空氣中的粉塵(二次揚塵)。
(4)有機物的不完全燃燒,如木材、焦油、煤炭等燃燒時所產生的煙。
(5)焊接作業中,由于焊藥分解,金屬蒸發所形成的煙塵。
9.生產環境,指異常的生產環境
(l)照明
工作區照度不足,照度均度不夠,亮度分布不當,光或色的對比度不當,以及存在頻閃效應、眩光效應。
(2)氣溫
工作區溫度過高、過低或急劇變化。
(3)氣流
工作區氣流速度過大、過小或急劇變化。
(4)濕度
工作區濕度過大或過小。
二、機械事故發生的直接、間接原因
一、機械事故發生的直接原因
1.機械的不安全狀態
(l)防護、保險、信號等裝置缺乏或有缺陷。
①無防護
無防護罩,無安全保險裝置,無報警裝置,無安全標志,無護欄或護欄損壞,設備電氣未接地,絕緣不良,噪聲大,無限位裝置等。
②防護不當
防護罩未在適當位置,防護裝置調整不當,安全距離不夠,電氣裝置帶電部分裸露等。
(2)設備、設施、工具、附件有缺陷。
①設備在非正常狀態下運行,設備帶“病”運轉,超負荷定轉等。
②維修、調整不良,設備失修,保養不當,設備失靈,未加潤滑油等。
③機械強度不夠,絕緣強度不夠,起吊重物的繩索不合安全要求等。
④設計不當,結構不合安全要求,制動裝置有缺陷,安全間距不夠,工件上有鋒利毛刺、毛邊、設備上有鋒利倒棱等。
(3)個人防護用品、用具。如防護服、手套、護目鏡及面罩、呼吸器官護具、安全帶、安全帽、安全鞋等缺少或有缺陷。
①所用防護用品、用具不符合安全要求。
②無個人防護用品、用具。
(4)生產場地環境不良
①通風不良
無通風,通風系統效率低等。
②照明光線不良
包括照度不足,作業場所煙霧煙塵彌漫、視物不清,光線過強,有眩光等。
③作業場地雜亂
工具、制品、材料堆放不安全。
④作業場所狹窄。
(5)操作工序設計或配置不安全,交叉作業過多。
(6)地面滑,地面有油或其他液體,有冰雪。地面有易滑物如圓柱形管子、料頭、滾珠等。
(7)交通線路的配置不安全。
(8)貯存方法不安全,堆放過高、不穩。
2.操作者的不安全行為
這些不安全行為可能是有意的或無意的。
(l)操作錯誤、忽視安全、忽視警告包括未經許可開動、關停、移動機器;開動、關停機器時未給信號;開關未鎖緊,造成意外轉動;忘記關閉設備;忽視警告標志、警告信號,操作錯誤(如按錯按鈕、閥門、搬手、把柄的操作方向相反);供料或送料速度過快,機械超速運轉;沖壓機作業時手伸進沖模;違章駕駛機動車;工件刀具緊固不牢.,用壓縮空氣吹鐵屑等。
(2)使用不安全設備。臨時使用不牢固的設施如工作梯,使用無安全裝置的設備,臨時拉線不符合安全要求等。
(3)機械運轉時加油、修理、檢查、調整、焊接或清掃。
(4)造成安全裝置失效。拆除了安全裝置,安全裝置失去作用。
調整錯誤造成安全裝置失效。
(5)用手代替工具操作。用手代替手動工具,用手清理切屑。不用夾具固定,用手拿工件進行機械加工等。
(6)攀、坐危險位置(如平臺護欄、吊車吊鉤等)。
(7)物體(成品、半成品、材料、工具、切屑和生產用品等)存放不當。
(8)穿不安全裝束如在有旋轉零部件的設備旁作業時穿著過于肥大、寬松的服裝、操縱帶有旋轉零部件的設備時戴手套,穿高跟鞋、涼鞋或拖鞋進入車間等。
(9)必須使用個人防護用品,用具的作業或場合中,忽視其使用,如未戴各種個人防護用品。
(10)無意或為排除故障而靠近危險部位,如在無防護罩的兩個相對運動零部件之間清理卡住物時,可能造成擠傷、夾斷、切斷、壓碎或人的肢體被卷進而造成嚴重的傷害。
二、間接原因
幾乎所有事故的間接原因都與人的錯誤有關,盡管與事故直接有關的操作人員并沒有出錯。這些間接原因可能是由于設計人員、設備制造、安裝調試、維護保養等人所犯的錯誤。間接原因包括:
1.技術和設計上的缺陷
工業構件、建筑物(如室內照明、通風)、機械設備、儀器儀表、工藝過程、操作方法、維修檢驗等的設計和材料使用等方面存在的問題。
(l)設計錯誤包括強度計算不準,材料選用不當,設備外觀不安全,結構設計不合理,操縱機構不當,未設計安全裝置等。即使設計人員選用的操縱器是正確的,如果在控制板上配置的位置不當,也可能使操作人員混淆而發生操作錯誤,或不適當地增加了操作人員的反應時間而忙中出錯。
設計人員還應注意作業環境設計,不適當的操作位置和勞動姿勢都可能引起操作人員疲勞或思想緊張而容易出錯。
(2)制造錯誤
即使設計是正確的,如果制造設備時發生錯誤,也會成為事故隱患。在生產關鍵性部件和組裝時,應特別注意防止發生錯誤。常見的制造錯誤有加工方法不當(如用鉚接代替焊接),加工精度不夠,裝配不當,裝錯或漏裝了零件,零件未固定或固定不牢。工件上的劃痕、壓痕、工具造成的傷痕以及加工粗糙可能造成用力集中而使設備在運行時出現故障。
(3)安裝錯誤
安裝時旋轉零件不同軸,軸與軸承、齒輪嚙合調整不好,過緊過松,設備不水平。地腳螺擰緊,設備內遺留工具、零件、棉紗等,都可能使設備發生故障。
(4)維修錯誤
沒有定時對運動部件加潤滑油,在發現零部件出現惡化現象時沒有按維修要求更換零部件,都是維修錯誤。當設備大修重新組裝時,可能會發生與新設備最初組裝時發生的類似錯誤。安全裝置是維修人員檢修的重點之一。安全裝置失效而未及時修理,設備超負荷運行而未制止,設備帶“病”運轉,都屬于維修不良。
2.管理缺陷
(l)無安全操作規程或安全規程不完善。
(2)規章制度執行不嚴,有章不循。
(3)對現場工作缺乏檢查或指導錯誤。
(4)勞動制度不合理
(5)缺乏監督。
3.教育培訓不夠,未經培訓上崗,操作者業務素質低,缺乏安全知識和自我保護能力,不懂安全操作技術,操作技能不熟練,工作時注意力不集中,工作態度不負責。受外界影響而情緒波動,不遵守操作規程,都是事故的間接原因。
4.對安全工作不重視,組織機構不健全,沒有建立或落實現代安全生產責任制。沒有或不認真實施事故防范措施,對事故隱患調查整改不力。關鍵是企業領導不重視。
三、機械設備的防范措施
一、危險性大的設備
根據事故統計。我國規定危險性比較大、事故率比較高的設備有:壓力機、沖床、剪床、壓正機、壓印機、木工刨床、木工鋸床、木工造型機、塑料注射成型機、煉膠機、壓磚機、農用脫料機、紙頁壓光機、起重設備、鍋爐、壓力容器、電氣設備等。
這些設備在出廠前必須配備好安全防護裝置。
二、機械的危險部位
操作人員易于接近的各種可動零、部件都是機械的危險部位,機械加工設備的加工區也是危險部位。
常見的危險零部位件有:
1.旋轉軸。
2.相對傳動部件如嚙合的明齒輪。
3.不連續的旋轉零件,如風機葉片,成對帶齒滾筒。
4.皮帶與皮帶輪,鏈與鏈輪。
5.旋轉的砂輪。
6.活動板和固定板之間靠近時的壓板。
7.往復式沖壓工具如沖頭和模具。
8.帶狀切割工具如帶鋸。
9.蝸輪和蝸桿。
10.高速旋轉運動部件的表面如離心機轉鼓。
11.聯接桿與鏈環之間的夾子。
12.旋轉的刀具刃具。
13.旋轉的曲軸和曲柄。
14.旋轉運動部件的凸出物,如鍵、定位螺絲。
15.旋轉的攪拌機、攪拌翅。
16.帶尖角、銳邊或利棱的零部件。
17.鋒利的工具。
18.帶有危險表面的旋轉圓筒如脫粒機。
19.運動皮帶上的金屬接頭(皮帶扣)。
20.飛輪。
21.聯軸節上的固定螺絲。
22.過熱過冷的表面。
23.電動工具的把柄。
24.設備表面上的毛刺、尖角、利棱、凹凸。
25.機械加工設備的工作區。
三、危險的作業
本身具有較大的危險性的作業稱為特種作業、其危險性和事故率比一般作業大。包括:
1.電工作業。
2.壓力容器操作。
3.鍋爐司爐。
4.高溫作業。
5.低溫作業。
6.粉塵作業。
7.金屬焊接氣割作業。
8,起重機械作業。
9.機動車輛駕駛。
10.高處作業等。
特種作業人員必須經過現代安全技術培訓、考核合格后才能上崗操作。
四、機械傷害形式
機械傷害的形式可分為8類:
l.咬入和擠壓
這種傷害是在兩個零部件之間產生的,其中一個或兩個是運動零部件,這時人體的四肢被卷進兩個部件的接觸處。
(l)擠壓
這種危險不一定兩個部件完全接觸,只要距離很近,四肢就可能受擠壓。除直線運動部件外,人手還可能在螺旋輸送機、塑料注射成型機中受擠壓。如果安裝距離過近或操作不當,如在轉動閥門的平輪或關閉防護罩時也會受擠壓。
(2)咬入(咬合)
典型的咬入點(也可叫擠壓點)是嚙合的明齒輪、皮帶與皮帶輪、鏈與鏈輪,兩個相反方向轉動的軋輥。一般是兩個運動部件直接接觸,將人的四肢卷進運轉中的咬人點。
2.碰撞和撞擊
這種傷害有兩種主要形式,一種是比較重的往復運動部件撞人,傷害程度與運動部件的質量和運動速度的乘積即部件的動量有關。另一種是飛來物及落下物的撞擊造成的傷害。飛來物主要指高速旋轉的零部件、工具、工件、緊固件固定不牢或松脫時,會以高速甩出。雖然這些物體質量很大,但轉速很高,而動能與速度的平方成正比,即動能很大。飛來物撞擊人體,能使人造成嚴重的傷害。高速飛出的切屑也能使人受到傷害。
3.接觸
當人體接觸機械的運動部件或運動部件直接接觸人體時都可能造成機械傷害。運動部件一般指具有銳邊、尖角、利棱的刀具,有凸出物的表面和摩擦表面;也包括過熱、過冷表面和電絕緣不良而導電的靜止物體的表面。后者不屬于機械傷害。接觸傷害有4類:
(l)夾斷
當人體伸入兩個接觸部件中間時,人的肢體可能被夾斷。夾斷與擠壓不同,夾斷發生在兩個部件的直接接觸,擠壓不一定完全接觸,兩個部件不一定是刀刃。其中一個是運動部件或兩個都是運動部件都能造成夾斷傷害。
(2)剪切
兩個具有銳利邊刃的部件,在一個或兩個部件運動時,能產生剪刀作用。當兩者靠近而人的四肢伸入時,刀刃能將四肢切斷。
(3)割傷和擦傷
這種傷害可以發生在運動機械和靜止設備上。當靜止設備上有尖角和銳邊,而人體與該設備作相對運動時,能被尖角和銳邊割傷。當然有尖角、銳邊的部件轉動時,對人造成的傷害更大,如人體接觸旋轉刀具、鋸片,都會造成嚴重的割傷。高速旋轉的粗糙面如砂輪能使人擦傷。
(4)卡住或纏住
具有卡住作用的部位是指靜止設備表面或運動部件上的尖角或凸出物。這些凸出物能絆住、纏住人寬松的衣服,甚至皮膚。當卡住后,有引向另一種危險,特別是運動部件上的凸出物、皮帶接頭、車床的轉軸、加工件都能將人的手套、衣袖、頭發、辮子甚至工作服口袋中擦機器用的綿紗纏住而使人造成嚴重傷害。
五、機械傷害的結果
機械傷害的后果一般比較嚴重,輕則損傷皮肉,重則斷肢致殘,甚至危及生命。GB6441—86((企業職工傷亡事故分類》對傷害后果有明確的規定。
GB6441—86規定以損失工作日來劃分傷害程度。損失工作日是指被傷害者失能的工作時問。
該規定對計算方法有嚴格的標準,計算損失工作日后即可確定傷害程度。其分類如下:
①輕傷
輕傷是指損失工作日為105—7天的失能傷害。
②重傷
重傷是指相當于現定損失工作日等于或超過105日的失能傷害。
③死亡
四、機械設備本質安全措施
一、本質安全的目的
本質安全化的目的是:運用現代科學技術,特別是安全科學的成就,從根本上消除能形成事故的主要條件;如果暫時達不到時,則采取兩種或兩種以上的相對安全措施,形成最佳組合的安全體系,達到最大限度的安全。同時盡可能采取完善的防護措施,增強人體對各種危害的抵抗能力。
二、本質安全化的內容
設備的本質安全措施可以通過設備本身和控制器的安全設計來實現。
l.本質安全化的基本思路
(l)從根本上消除發生事故的條件。許多機械事故是由于人體接觸了危險點、如果將危險操作采用自動控制、用專用工具代替人手操作,實現機械化等都是保證人身安全的有效措施。
(2)設備能自動防止操作失誤和設備故障。設備應有自動防范措施,以避免發生事故。這些措施應能達到:即使操作失誤,也不會導致設備發生事故.即使出現故障,應能自動排除,切換或安全停機;當設備發生故障時,不論操作人員是否發現,設備應能自動報警,并作出應急反應,更理想的是還能顯示設備發生故障的部位。
2.常用的措施
(l)采用機械化、自動化和遙控技術。
(2)采用可靠性設計,提高機械設備的可靠性。詳見下一節。
(3)采用安全防護裝置。當無法消除危險因素時,采用安全防護裝置隔離危險因素是最常用的技術措施。
(4)安裝保險裝置。保險裝置又叫故障保險裝置。這種裝置的作用與安全防護裝置稍有不同。它能在設備產生超壓、超溫、超速、超載、超位等危險因素時,進行自動控制并消除或減弱上述危險。安全閥、單向閥、超載保護裝置、限速器、限位開關、爆破片、熔斷器、保險絲、力短限制器、極限位置限制器等都是常用的保險裝置。
(5)采用自監測、報警和處理系統。利用現代化儀器儀表對運行中的設備狀態參數進行在線監測和故障診斷。
(6)采用冗余技術。冗余技術是可靠性設計常采用的一種技術,即在設計中增加冗余元件或冗余(備用)設備,平時只用其中一個,當發生事故時,冗余設備或冗余元件能自動切換。
(7)采用傳感技術。在危險區設置光電式、感應式、壓力傳感式傳感器,當人進入危險區,可立即停機,終止危險運動。
(8)安裝緊急停車開關。
(9)向操作者提供機械關鍵安全功能是否正常(設備的自檢功能)的信息。
(10)設計程序聯鎖開關。設計對出現錯誤指令時,禁止啟動的操縱器。這些關鍵程序只有在正常操作指令下才能啟動機械。
(ll)配備使操作者容易觀察的、能顯示設備運行狀態和故障的顯示器。
(12)采用多重安全保障措施。對于危險性大的作業,要求設備運行絕對安全可靠。
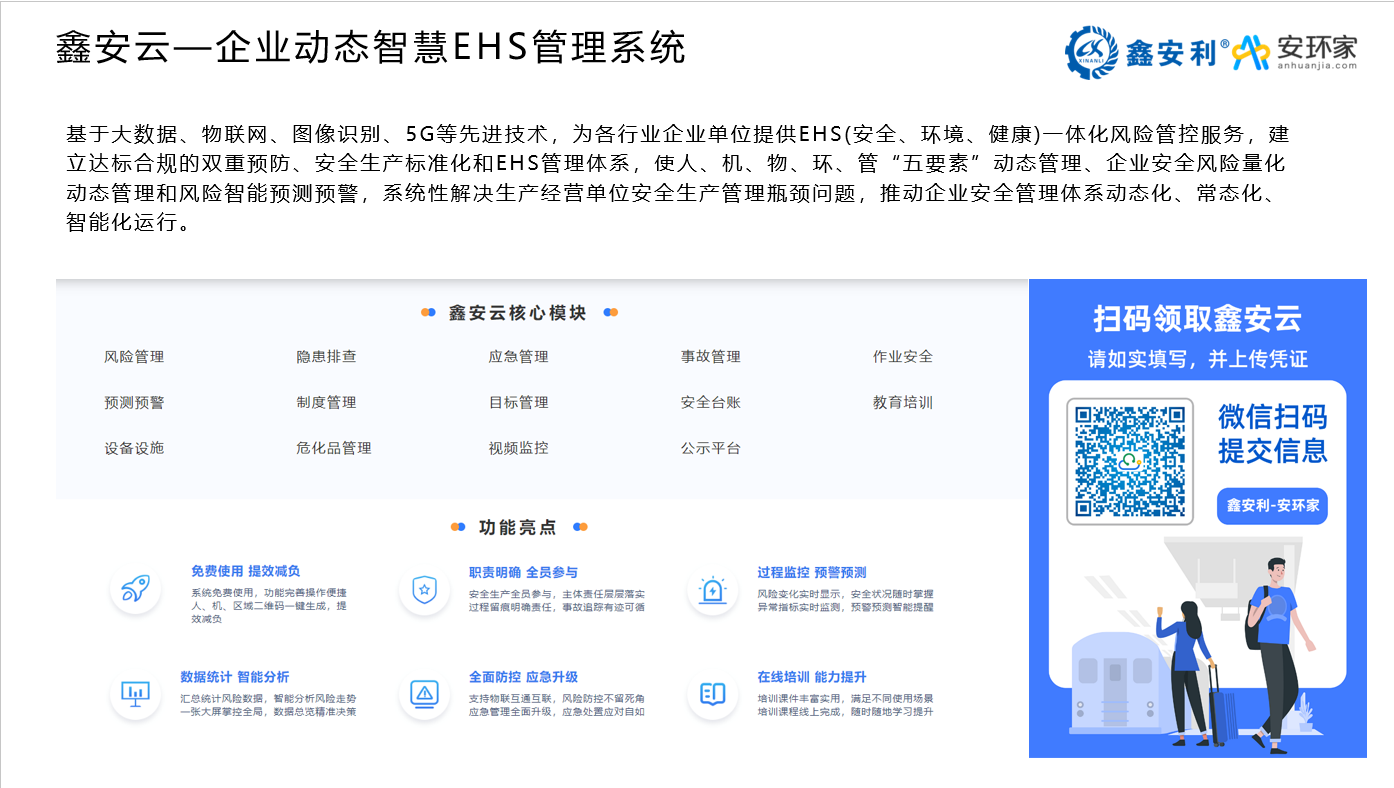