1 總則
1.1 為使涂漆前處理作業符合勞動安全衛生要求,保障作業人員的安全和健康,保護環境,促進生產建設發展,特制訂本規程。
1.2 本規程適用于室內進行的金屬表面涂漆前處理作業;在室外進行的船舶、機車車輛、大型金屬構件(如:電視塔、鋼結構橋梁等)的涂漆前處理作業,可參照本規程的原則,結合實際條件,制訂相應的安全技術要求和措施。
1.3 涂漆企業(車間、工段)的涂漆前處理工藝應采用先進技術,以無塵毒或低塵毒、低噪聲、不需防火防爆的安全工藝代替有塵毒、高噪聲、易爆、易燃的不安全工藝,逐步實現管道化、密閉化和自動化。
2 作業場所
2.1 車間(工段)涂漆前處理作業的場所,應設置在廠區夏季最小頻率風向的上風側,并宜與生產過程相銜接的鈑焊、機械加工、裝配、金屬材料庫、成品庫分隔。
2.2 車間(工段)涂漆前處理作業場所,宜布置在單跨單層建筑物內,當不得不布置在多跨建筑物內時,應一側近外墻。
2.3 用有機溶劑除油、除舊漆的前處理作業場所,屬于甲、乙類火災危險性生產區域。作業場所應有泄壓面積,其面積與廠房體積的比值,及與相鄰生產車間建筑物的防火間距,建筑物防爆,以及消防車道等,均應符合TJ16-74《建筑設計防火規范》。
2.4 用有機溶劑除油、除舊漆的作業場所必須有良好的通風,嚴禁吸煙和引入火種,作業過程中不準電瓶車、汽車和金屬輪車進入。
2.5 在距離有機溶劑除油、除舊漆作業場所外界的水平方向和垂直方向3m范圍內,屬于1級爆炸危險場所,不宜設置電氣設備;當采用良好通風裝置并有聯鎖保護后,降低為2級;在相距水平和水平方向3m以外的場所降低一級。作業場所的電氣設備,應符合有關爆炸危險場所電氣安全規定。
2.6 車間(工段)前處理作業場所的圍護結構的內壁面宜涂淺色涂料,當采用腐蝕性處理液時,屋梁、屋面及墻壁應涂覆防腐涂料。
2.7 車間(工段)涂漆前處理作業場所的地面應平整防滑,易于清掃、不滲水積水。經常有酸堿液流散或積聚的地面,應采用耐腐蝕材料敷設,并裝置沖洗地面和墻壁的設施,廢水應能排向廢水處理系統。
有機溶劑漆前處理場所宜采用不發火花的地面,地坪建筑設計應符合國家有關地坪設計的規定。
2.8 用有機溶劑除油、除舊漆工作位置周圍15m范圍內,用機動工具除銹工作位置周圍5m范圍內,均嚴禁堆積易燃、易爆物料,當不能滿足上述要求時,應設防火墻或防火帶等阻隔措施。
2.9 與高壓噴射清洗裝置配套的泵、配件及管路系統和噴丸除銹(或除舊漆)裝置的筒體和橡膠軟
國家標準局1987-04-20批準1987-12-01實施GB 7692-87管,應按國家有關規定作耐壓試驗和密封性試驗。
2.10 涂漆前處理作業用的手持照明燈具,應符合GB 3805-83《安全電壓》的規定。
3 作業勞動衛生
3.1 車間(工段)涂漆前處理作業場所的夏季空氣溫度,應符合TJ 36-79《工業企業設計衛生標準》中第49條規定,冬季根據生產需要和機械排風狀況在封閉的手工操作區域相應采取局部采暖,以保持作業區環境溫度不低于12℃。
3.2 車間(工段)涂漆前處理作業場所的天然光照度最低值為50lx;采光系數最低值為1%;惟磷化膜和鈍化膜質量檢測區域的室內天然光照度最低值為100lx,采光系數最低值為2%。
3.3 車間(工段)涂漆前處理作業場所當采用混合照明時,最低照度為150lx;采用一般照明時,最低照度為50lx;惟磷化膜和鈍化膜質量檢測區域內,當采用混合照明時為500lx,一般照度為150lx。
3.4 涂漆前處理作業場所,空氣中有害物質的最高容許濃度,應符合TJ 36-79規定。
3.5 涂漆前處理作業場所的各項設備應采取減振、隔聲、消聲、吸聲等項措施使操作區的噪聲級不超過衛生部、(原)國家勞動總局頒發的《工業企業噪聲設計衛生標準(試行草案)》的規定。
3.6 車間(工段)涂漆前處理作業場所應設置更衣室、休息室和吸煙室,并在其附近設置(車間)浴室和事故應急沖洗用水,供水壓力根據需要確定,最高不超過1.76×10^5Pa;應配有快開閥門和長度1.2m以上的軟管。
3.7 涂漆前處理作業場所的衛生特征級別為2級。
3.8 涂漆前處理機械除銹限制使用干噴砂,應用真空噴砂、濕式噴砂、噴丸和拋丸代替,當工藝有特殊要求,上述工藝方法不能代替時,允許使用干噴砂,但應在密閉箱內進行,并必須隔離操作。
3.9 涂漆前處理作業中嚴禁使用苯。
3.10 大面積除油和清除舊漆作業中,禁止使用甲苯、二甲苯和汽油,應分別采用水基清洗液或堿液和水沖型脫漆劑代替。
3.11 涂漆前處理作業中產生的漂洗水、沖淋水、廢液和廢酸的排放,應符合GB J4-73《工業三廢排放試行標準》的規定。
3.12 機械方法除銹或清除舊漆必須設置獨立的排風系統和除塵裝置,對于大中城市排放至大氣中的粉塵含量不大于150mg/m^3。
3.13 涂漆前處理車間(工段)的化學藥品存放量不許超過兩個工作班的需要量。藥品儲存柜應靠近使用點。
3.14 涂漆前處理作業人員應按國家有關勞動保護規定穿戴個人防護用品,當進行噴丸、除舊漆操作時應佩戴長管面具。
4 除油清洗
4.1 用可燃性有機溶劑除油時,應先拆去產品或部件上的蓄電池或其他電源裝置;其作業場所應設有醒目標牌,并配置可燃氣體快速測量儀,定期檢測。
4.2 用可燃性有機溶劑除油清洗作業完畢,必須將廢料集中移放于指定的安全地點。
4.3 供除油清洗用的機動工具,所配置的電機、電器、照明燈具等宜采用密閉型,防止清洗液濺入。
4.4 大型浸漬清洗槽應配置起重設備,橋式和梁式起重機的駕駛室應避開清洗槽。向浸洗槽中吊裝工件時應采用起重設備吊鉤和專用工具,嚴禁操作人員直接用手搬運或使用鋼絲繩吊裝。
4.5 大型浸漬清洗槽的槽口宜高出地面0.8m,并配置活動網蓋。當槽體全部埋入地面時,在槽邊四周應按GB 4053.3-83《固定式工業防護欄桿》設置防護欄桿。并按GB 2894-82《安全標志》的規定,設置警告標志。
4.6 采用水基清洗液或堿液的大型浸漬清洗槽,其槽體內底部宜設置活動底盤或金屬網架,便于清除污泥。同時宜設置配料槽,配料槽上加蓋封閉,蓋上設置開啟門。
4.7 噴淋除油清洗的結構應為密閉式或半封閉式,制件出入口兩端應設置防清洗液飛濺的屏幕室,屏幕室的門洞用擋簾隔開,并設置獨立的排風系統。
4.8 高壓噴射清洗裝置應配置油壓、水壓壓力控制和聯鎖裝置,并與驅動高壓水泵用的主動電動機聯鎖。
4.9 長臂高壓噴槍必須配置自鎖安全機構,噴射間歇應將噴槍自鎖。
4.10 高壓水泵短期停止工作時,必須清洗保養,重行使用前應檢查各處密封質量,并作耐壓試驗。
4.11 氣相除油清洗可利用半封閉槽進行,應有嚴格的防止清洗液蒸氣逸出的措施;槽體內壁襯里材料宜用不銹鋼、陶瓷、阻燃型不飽和聚酯樹脂玻璃鋼。
4.12 氣相除油清洗裝置應具有清洗液的溫度和液位的自動控制、監視,以及冷凝器冷卻水的供水監視器,其中測溫用溫度計的分度值應不大于0.5℃。
4.13 超聲波除油清洗用的清洗槽,長期受空化腐蝕,必須定期檢查,防止槽底破裂事故。
5 除銹
5.1 中小型工件機械除銹應優先選用真空噴砂或濕式噴砂;大件應優先選用噴丸和拋丸,實現除銹過程密閉化,改善勞動條件。
5.2 手工除銹鋼刷、鏟刀和鐵錘等工具,作業前應檢查可靠性。相鄰操作人員的間距宜為1m。
5.3 凡離地2m以上進行手工除銹作業,必須設置腳手板及其扣掛繩索,腳手板應采用金屬鏤空結構等防滑措施,腳手板和坐身板應牢固平穩。工具放置固定可靠,不使墜落。
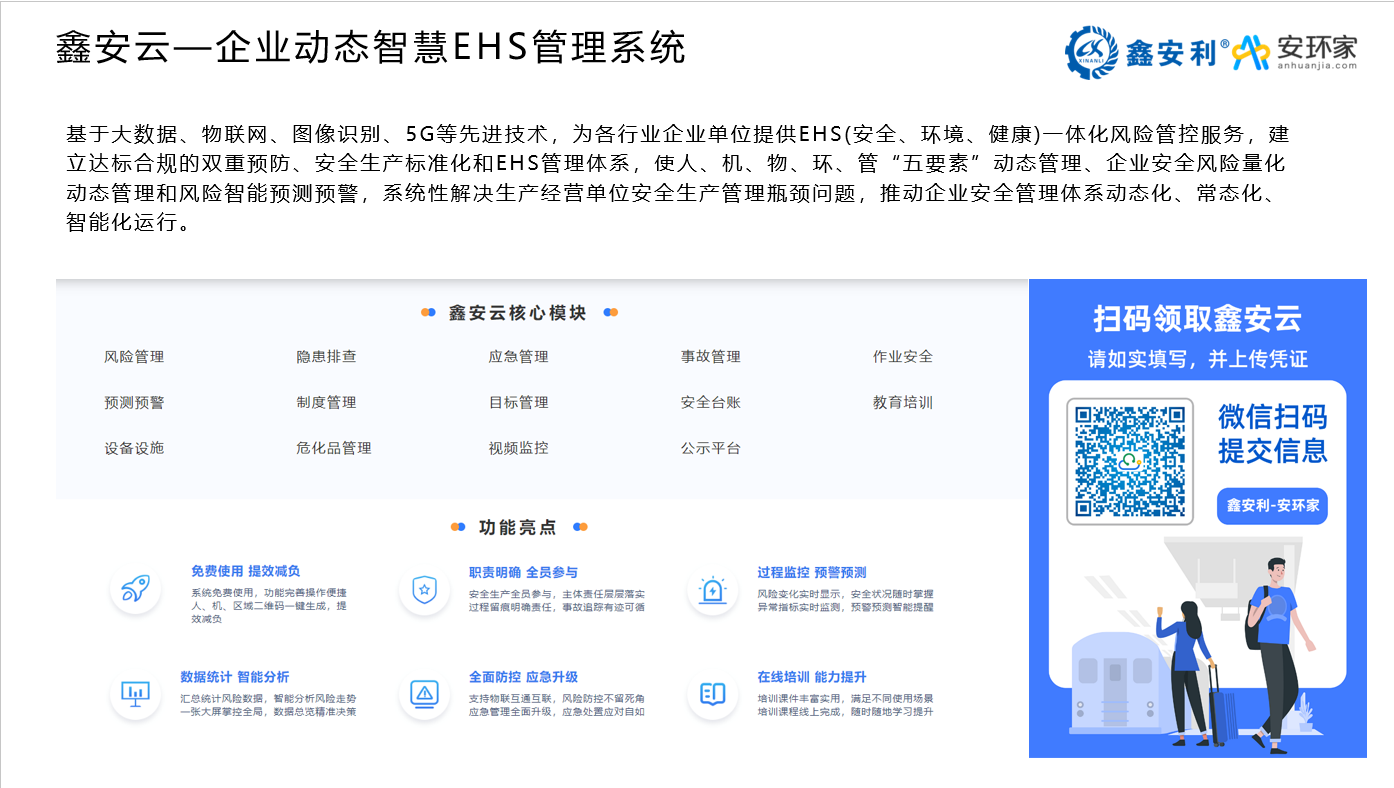