一、裝置簡介
(一)裝置發展及類型
1.裝置發展
現代煉油工業的加氫技術(包括加氫工藝、催化劑和專用設備)是在第二次世界大戰以前經典的煤和煤焦油高壓催化加氫技術的基礎上發展起來的。1949年鉑重整技術的發明和工業應用,除生產大量高辛烷值汽油組分外還副產大量廉價的氫氣,對現代加氫技術的發明和發展起到了關鍵作用。
1950年煉油廠出現了加氫精制裝置,1959年出現了加氫裂化裝置,1963年出現了沸騰床渣油低轉化率加氫裂化裝置,1969年出現了固定床重油加氫脫硫裝置,1977年出現了固定床渣油加氫脫硫裝置,1984年出現了沸騰床渣油高轉化率加氫裂化裝置。這些加氫技術的發明和工業應用,使加氫技術由發生、發展走向成熟。加氫(包括加氫裂化、加氫精制和加氫處理)成為世界上加工能力最大的二次加32212藝,是煉油工業的三大支柱技術(加氫、催化裂化和催化重整)之一。
生產低硫、低芳烴和高十六烷值的優質柴油是當前世界范圍內車用柴油燃料的生產趨勢,也已成為國內各石化企業正在面臨的挑戰。中石化股份公司已在2003年提出在國內實施《城市車用柴油》標準(Q/SHll008—2002),其主要質量指標:硫質量分數不大于0.030%,總芳烴質量分數不大于25%,多環芳烴質量分數不大于5%。歐洲提出2005年將要求硫含量小于50X10—6,世界燃料規范Ⅲ類柴油的硫含量指標是30X10—6。近幾年,國內外文獻報道有許多關于未來柴油規格的研究和推測,更低的柴油硫規格的推廣正在加速。所以研究開發能夠生產低硫、低芳烴和高十六烷值的優質柴油的催化劑成為柴油加氫的主要發展方向。本節主要以柴油加氫精制裝置展開討論說明。???
2.裝置的主要類型
加氫精制是各種油品在氫壓下進行改質的一個總稱。加氫精制處理原料油范圍寬,產品靈活性大,液體產品收率高質量好。加氫精制的目的主要是對油品進行脫硫、脫氮、脫氧、烯烴飽和、芳烴飽和和脫除金屬、瀝青雜質等,以達到改善油晶的氣味、顏色和安定性,防止腐蝕,進一步提高產品質量,滿足油品的使用要求。
加氫精制工藝裝置主要類型有:石腦油加氫、煤油加氫、柴油加氫、潤滑油加氫和石蠟加氫等。還可以對劣質渣油進行加氫處理,得到安全性好的低硫、低黏度的餾分,除生產部分石腦油和優質柴油外,其重組分可做重油催化裂化的原料。
加氫精制工藝操作條件視原料性質而定,一般反應總壓力為3.0~8.0MPa之間。反應溫度300—360°C,液時空速1.0~2.0之間。渣油加氫工藝條件要求苛刻,如孤島減壓渣油加氫要求壓力高達16.9MPa,溫度385%。隨著加氫工業技術的發展,我國加氫催化劑水平也有很大的發展,基本上能滿足煉油廠加氫精制的要求。
二、重點部位及設備
(一)重點部位
1.反應系統
反應系統主要有加熱爐、加氫反應器和高壓分離器三部分組成。
(1)加熱爐采用純燒瓦斯的方箱式加熱爐,雙排管雙面輻射,一旦有問題,直接影響反應溫度和產品的質量。
(2)反應器分三個床層,其中第一床層上部加有一層保護劑,其余三層為加氫催化劑。在第二床和第三床層入口設有急冷氫,防止催化劑的結焦和床層超溫或“飛溫”。反應器是裝置的心臟,一旦出現問題直接導致裝置的停工。
(3)高壓分離器主要是將反應產物分離為循環氫、低分油和含硫含氨污水(酸性水)部分。高分器液位超高可以導致循環氫帶液危害壓縮機的正常運行;如低液位,或液位抽空,會使高壓氣竄人低分器,導致惡性爆炸事故發生。
反應部分屬于高壓高溫部位,在選材時要考慮耐高壓高溫和耐腐蝕,一旦出現問題將影響正常生產。
2.產品分離
(1)低壓分離器
低壓分離器是將高壓分離器減壓分離后的油進一步分離,把燃料氣和酸性水脫除,降低汽提塔的負荷。由于酸性氣和酸性水有很強的腐蝕性,因此在選材時一定要選耐腐蝕的材質。
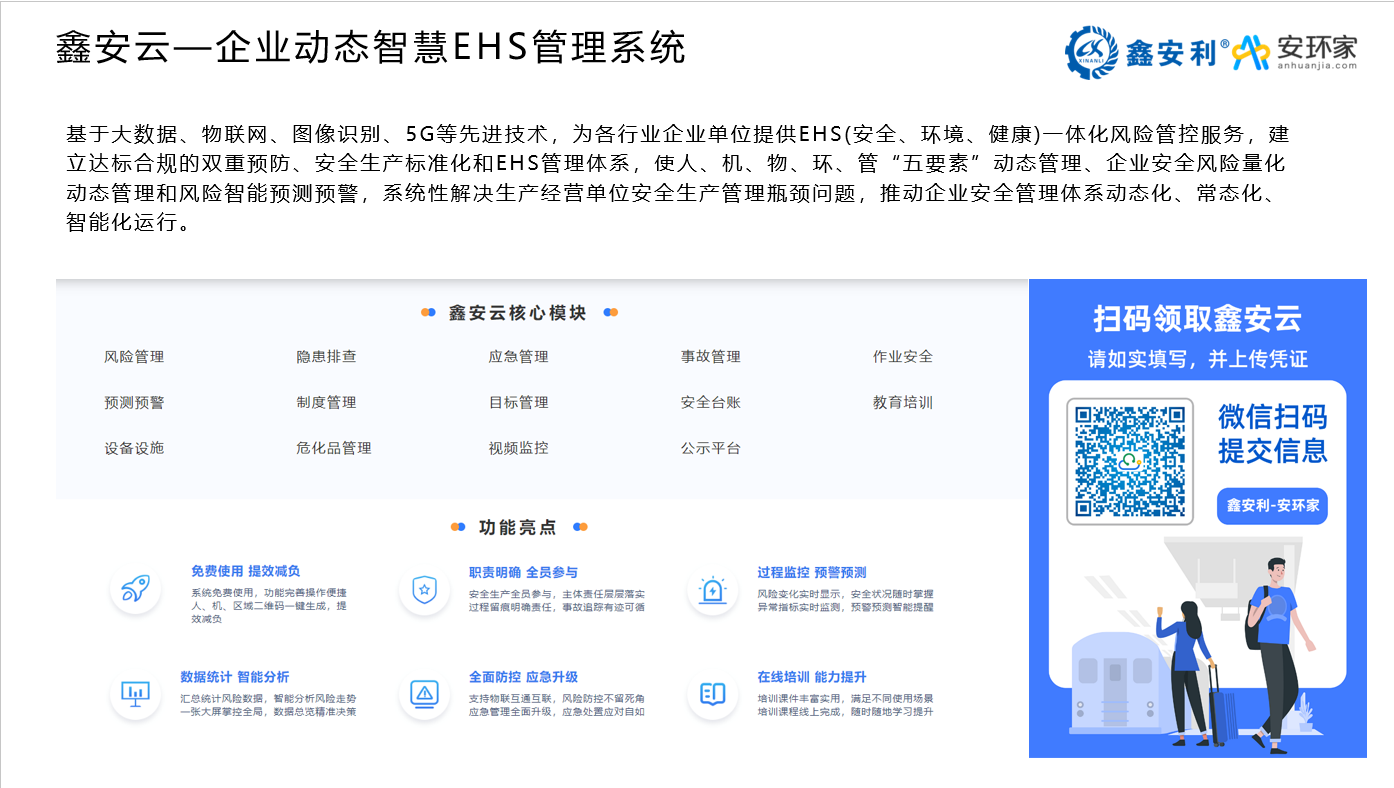