石油化工生產中使用的原材料(包括成品及半成品)大多易燃、易爆、易腐蝕,生產過程伴有高溫、高壓及深冷,工藝操作連續化,化學反應復雜,生產設備繁多,易形成爆炸混合物,且生產中使用的電源、火源及其他熱源較多,故石油化工生產具有火災及爆炸危險性。國內外火災案例亦已證明,一旦石油化工企業發生火災,就可能造成嚴重經濟損失和較大人員傷亡,并造成惡劣的社會影響,因此,分析石油化工企業火災的原因,采取相應的預防對策,做好防火工作,以達到控制火災發生,減少火災損失的目的,應成為消防安全工作的一項重要內容。筆者跟蹤調查了特大型石油化工企業——揚子石化公司自1991年至1999年發生的火災事故,分析了9年中共發生的122起生產火災,找出了引發火災事故的主要原因,并提出了相應的預防對策,以期有助于進一步做好石油化工企業的防火工作。
??? 引發火災的主要原因
每起石油化工火災的燃燒物、點火源、火勢及損失各不相同,但究其成因,許多火災有類似之處,通過分析可以看出,引發火災的主要原因為:
一、設備泄漏。分析結果表明,設備泄漏是引發石油化工火災最主要的原因。122起火災中由于泄漏引發的有42起,占總起數的34.43%。設備泄漏與設備設計、設備材質、檢修質量及工藝特點有直接關系。設備泄漏有三個因素:受熱影響、受載荷影響或材質性能下降。設備泄漏引發火災甚至裝置停車的例子很多。如本公司煉油廠在1995年發生的10起火災中就有8起是由于設備泄漏引發的。
二、違章動火。石油化工企業在生產、檢修過程中少不了動火,而因違章動火引發的火災也占很大比例。9年中揚子公司共發生22起因違章動火引起的火災,占總起數的18.03%。違章動火體現在兩方面:1.領導違章指揮。為了生產、檢修進度,一些領導不顧或忽視安全規定,在不具備動火的條件下指揮人員動火。2.職工盲目動火。有的職工不熟悉動火管理規定,或存在僥幸心理,不辦動火手續,不采取措施清除可燃物,在不備滅火器材、無人在現場監護的情況下盲目動火,引發火災。
三、誤操作。石油化工企業大多生產規模大,工藝流程復雜,工藝參數多,這就給操作帶來難度,而9年中揚子公司火災事故表明,誤操作是引發火災的又一重要原因。由于操作引發的火災共19起,占總起數15.258%。誤操作有管理上的問題也有操作人員業務素質上的問題等。誤操作表現為錯開(閉)閥門,或未關嚴閥門,該置換的容器及管道未置換或置換不徹底,或不采取有效措施拆卸設備等,這就造成流程走向錯誤,設備超壓、超溫、物料泄漏,最終導致火災。例如:1992年7月18日,本公司煉油廠裂解車間TA—1324污油罐發生著火爆炸事故,398名消防官兵參戰,出車37臺次用了2小時才將大火撲滅,直接經濟損失4.74萬元。究其原因是由于職工張某誤操作使高壓蒸汽串入吹掃線,導致油罐渣油冒頂,被溫度高達340℃的吹掃管線引燃造成的。
四、電氣故障。由于設計、選型錯誤,安裝、使用不當,設備線路老化,防雷、防靜電設施不全等電氣故障引發的火災在石油化工企業火災中也占有較大比例。揚子公司9年中因電氣故障引發的火災就有18起,占總起數的14.75%。如1994年8月9日,芳烴廠給排水車間2600 #的隔油池A2601發生火災,消防隊出動12臺車,用30分鐘才將大火撲滅。調查發現,火災就是因為某溶助劑廠擅自使用非防爆型泥漿泵清理油池時,產生電火花引燃了油蒸氣造成的。
五、自燃。由于生產中高溫表面多,采用高壓壓縮工藝,以及一些物質的本身性質,石油化工企業都有可能發生因自燃而引起的火災,9年中揚子公司共發生此類火災12起,占總起數9.84%。如催化劑三乙基鋁自燃、聚丙烯自燃等。
9年中,由于設備泄漏,違章動火、誤操作、電氣故障、自燃五方面的原因引發的火災共為113起,占總起數的92.62%,這足以說明這五方面原因是引發石油化工企業火災事故的主要原因。
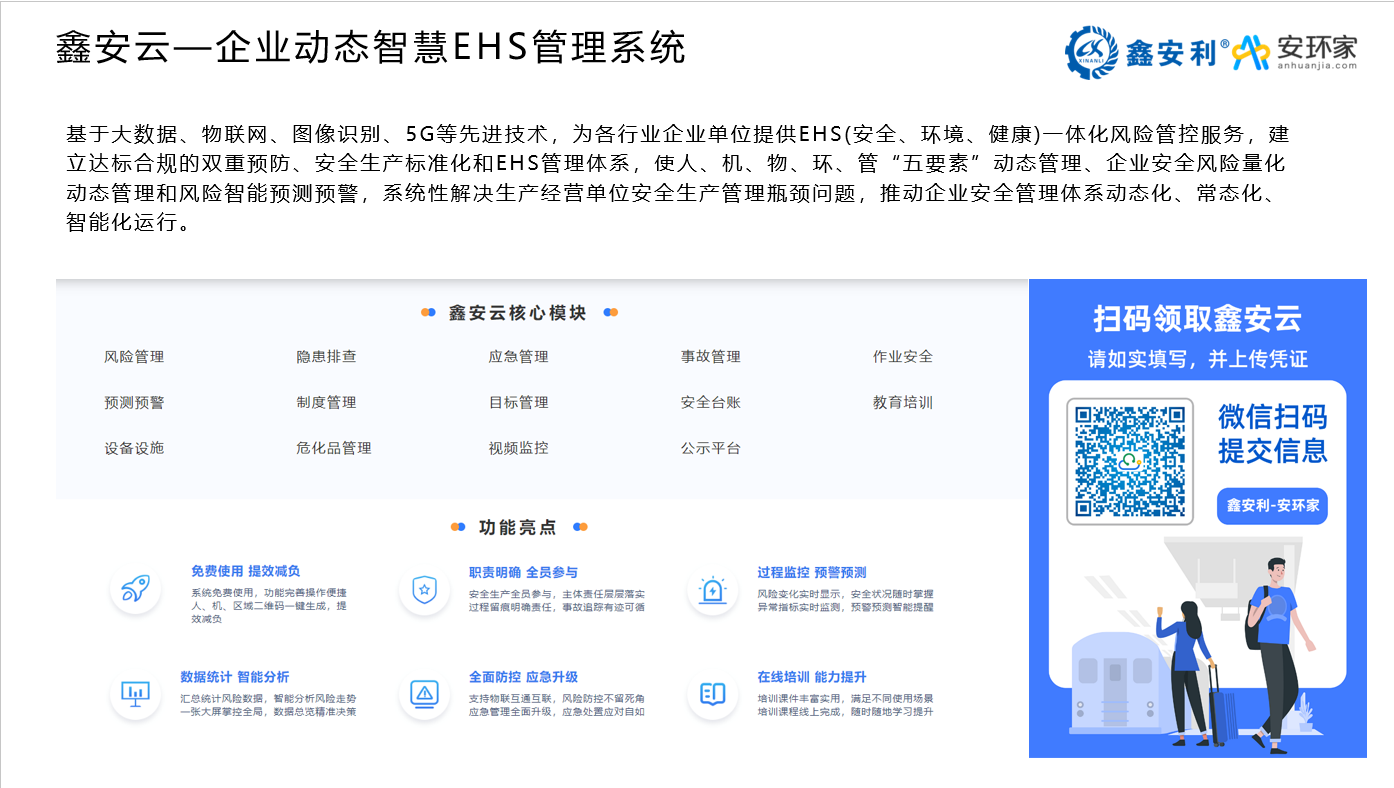