?前言(一)
??? 天津大沽化工有限責任公司作為國家重要的化工生產基地,多年來一直非常重視產品的技術引進及消化,其主導產品的產量連年大幅度提高,特別是聚氯乙烯產量由1995年8萬t/a增加到2001年的20萬t/a。為進一步鞏固聚氯乙烯產量在國內市場的主導地位,大幅度降低成本,提高經濟效益,公司決定從日本引進具有當今世界先進水平的2套108m3聚合釜裝置,安裝在前次技術改造預留的兩個62.5m3聚合釜安裝孔位置(原設計為4臺62.5m3聚合釜安裝位,現已安裝2臺62.5m3聚合釜,并已投入使用)。
108m3聚合釜技術參數如下:
重量:67t,外形尺寸:ф4400mm×10740mm
支腿處最大直徑為φ5300mm
62.5m3聚合釜安裝預留孔尺寸為5000mm×5000mm,框架樓一層橫梁高度為6m。可見,預留孔尺寸與聚合釜外形尺寸很接近,在不破壞框架主要結構的情況下,施工會有很大困難。
起重運輸及吊裝過程簡介(二)
??? 第一過程:卸船。2臺108m3聚合釜首先由日本船運至天津新港,再從新港拖輪船載運至公司自備碼頭,最后聚合釜由外租浮吊卸至碼頭。
第二過程:滾運。由于運輸現場不允許大型工程機械作業,因此必須采取滾運方法運輸。聚合釜由碼頭運輸至安裝孔位置,必須經過調轉5次90°方向,長約350m的距離且3次通過高度不足的管廊。
第三過程:吊裝。兩套自制龍門架分別拴掛聚合釜頭、尾部,使其由運輸時的臥式起吊旋轉90°成直立狀態,而后起升至底部距離地面2.5m,然后逆時針旋轉45°安裝臨時支撐腿。期間在設計安裝支腿位置進行混凝土支腿澆注,待保養期過后,聚合釜再回轉45°進行定位安裝。
注:在聚合釜吊裝過程中,其東側轉化器裝置、西側兩臺62.5m3聚合釜正常開車,必須采取相應安全措施。
施工過程危險因素分析(三)
??? 1.卸船過程危險因素分析
1.1由于外租浮吊違章作業及其他因素引起的聚合釜損壞。
1.2公司自備碼頭為非起重接卸碼頭,2臺聚合釜可能造成碼頭局部超載。
1.3由于碼頭位于廠區邊緣,非本公司職工及作業人員較多,且施工場所面積有限,各類人員容易受到傷害。
1.4聚合釜釜體周圍有10余個用于聯接冷卻循環、出入料等用途的法蘭盤,卸船過程中應避免法蘭盤受損。
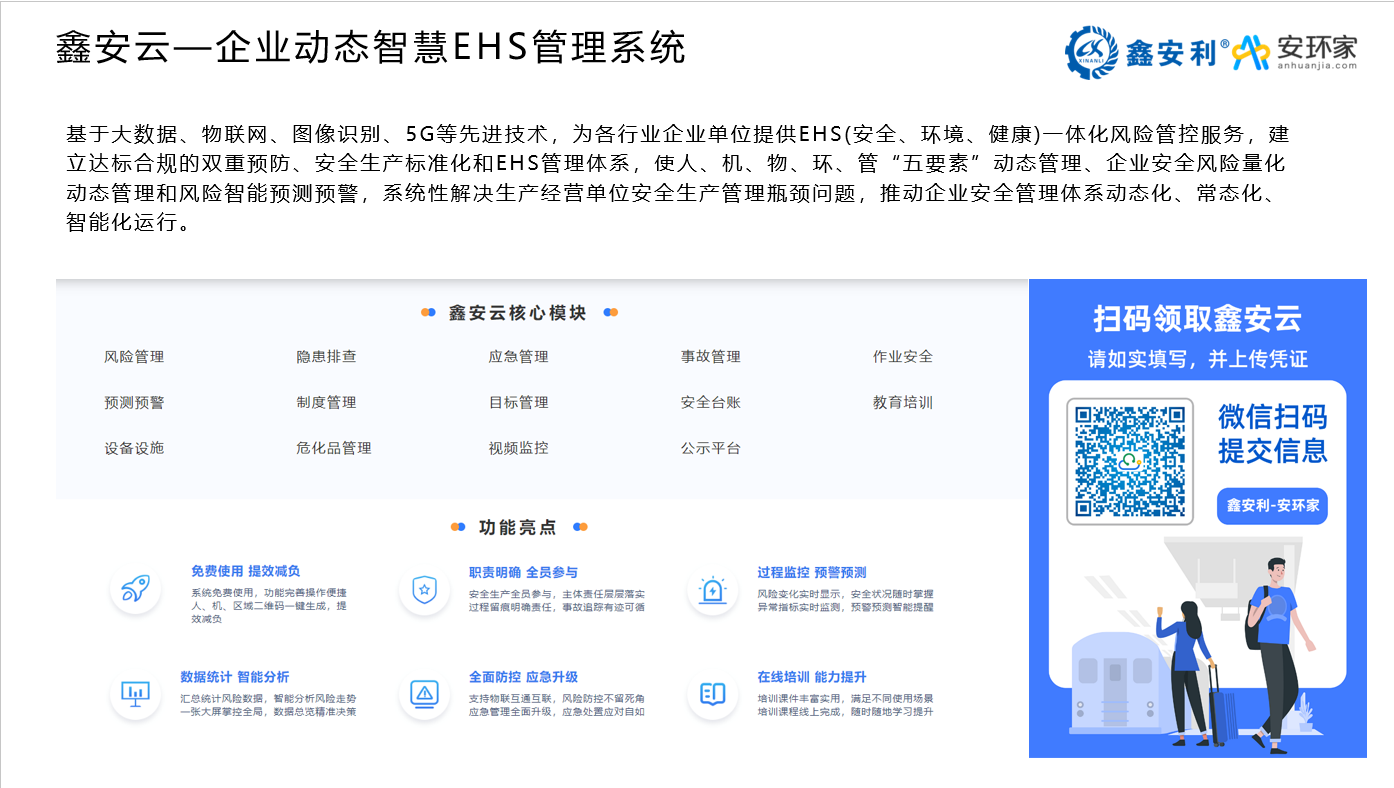