催化裂化是蠟油和渣油在高溫和催化劑作用下,在提升管式反應器中進行快速反應,把較大分子的烴類裂化為較小分子烴類,再經分餾、吸收等工序生產汽油、柴油、液態烴干汽等產品的煉油生產裝置。催化裂化反應類型主要有裂化反應、異構化反應、氫轉移反應和芳構化反應四種。反應—再生和分餾是催化裂化裝置的核心。裝置除具有易燃、易爆、易中毒特點外,油漿易結焦堵塞設備管線,也是比較突出的安全問題。
(一)反應—再生單元安全特性
在反應—再生過程中,原料油與再生后的高溫催化劑在反應器提升管的下部進入并呈沸騰流化狀態(催化劑為固體)接觸反應,反應后的催化劑和油氣經上部的反應沉降器進行氣固分離,反應油氣去分餾。催化劑由斜管回到燒焦罐燒焦。在燒焦罐中,反應后催化劑自待生斜管進入燒焦罐底部,在壓縮空氣推動下呈沸騰流化狀態進行燒焦,并由主風帶入上部再生器進一步燒焦。再生后的高溫催化劑由再生斜管進入提升管式反應器底部流化反應。在這個反應—再生過程中,同時存在著易燃物(反應油氣)、助燃物(壓縮空氣)和燒焦明火三個要素。所以在實際操作中必須嚴格控制汽提段流量和二段流量。
另外,如果沉降器頂壓過高,不僅會迫使系統停車,甚至可能會使催化劑倒流引發重大事故。
(二)反應再生過程操作異常現象
(1)提升管溫度大幅度波動,會燒壞設備。引起溫度大幅度波動的原因主要有:流量波動大或原料帶水;燒焦罐溫度大幅度波動;原料預熱溫度大幅度波動;兩器差壓波動;催化劑量波動;再生滑閥控制失靈。
對溫度波動要查明原因,有針對性地采取措施。如對原料進行脫水,穩定進料量和原料預熱溫度,穩定燒焦溫度,調節兩器差壓。如儀表失靈改用手動等。
(2)沉降器壓力大幅波動。如果沉降器出現壓力大幅度波動,首先要準確判斷異常原因,采取對應的處理措施。如果是原料帶水,要立即進行脫水。進料量波動大時要穩定進料量。其它原因如汽提蒸汽量及壓力波動大,催化劑循環波動量大,以及分餾塔釜液位過高等,都要及時采取對應的調節控制措施。
(3)再生器壓力大幅度波動。原因主要有:雙動滑閥失控、主風量波動大、外取熱器取熱管破裂、待生劑帶油、進入再生器水蒸氣壓力流量大幅度變化、啟用燃燒油過猛或帶水。
處理時要根據產生異常現象的原因采取措施。如滑閥失控可改為手動控制或搖控;風量波動可調節主風機入口蝶閥以穩定風量;外取熱器管破裂則可停掉破裂的取熱管束;待生劑帶油時可加大汽提蒸汽;進再生器的蒸汽壓力和流量波動大時,可調節穩定進再生器的蒸汽壓力和流量;如果燃油帶水或噴油過猛,則要對燃油脫水和緩慢噴燃燒油。
(4)催化劑架橋,影響催化劑的流動。通常可用如下方法處理:適當調節蒸汽量,降低汽提段料位;加強蒸汽冷凝液排除;適當開大再生滑閥,增加催化劑循環量,調整斜管蒸汽。
(三)分餾單元操作
分餾塔塔底液位過高,會造成沖塔和油氣管液封,使反應器超壓停車。如果分餾塔頂油氣分離器液面過高,則會使富氣帶液損壞氣壓機。所以分餾液位控制十分重要。如果出現塔底液位突然上漲,應判明原因及時處理。處理方法通常有:
(1)聯系反應崗位降量、提高反應深度。
(2)降低油漿循環量和回煉油返塔量。如因回煉油罐溢出,流入塔底引起的,則要加大回煉比,提高油漿回煉量。
(3)切換備用泵或解決油漿泵抽空氣阻問題。
(4)以上措施不見效時應聯系外甩油漿。
另外,如果塔釜的塔盤結焦堵塞,應考慮清理疏通。
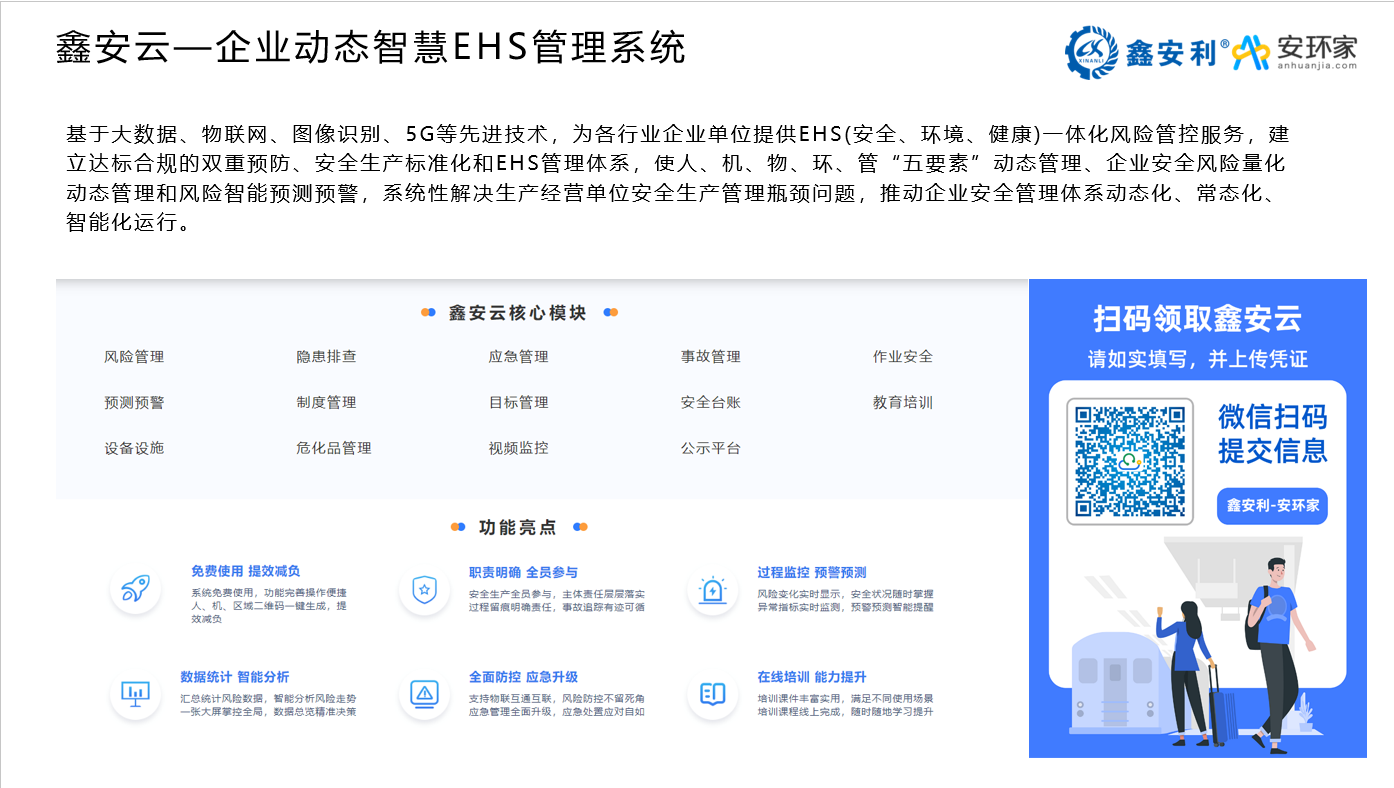