作者:鄭軍 張延斌
原有粗氨水蒸餾塔為一變徑板式塔,塔板為F1型浮閥塔板。其中1~24層(自下而上)塔徑為2000mm,塔板為傳統弓形雙溢流塔板;25~30層塔徑為1200mm,塔板為傳統單溢流塔板。
氨含量為5000mg/L(其中游離氨濃度為4000mg/L,固定氨為800mg/L)左右的稀氨水以70t/h的流量進入粗氨水蒸餾塔第24層塔板,從塔中部第12層板采出濃度為12%的濃氨水。該裝置在實際運行中主要存在如下問題:
(1)原料廢水中氨含量受氣化所用煤質的影響經常超標,通常情況在5500~1000mg/L間波動,造成塔釜廢水氨含量經常在300~1000mg/L之間徘徊,嚴重影響了后續生化處理的操作,使生化處理排放水中氨氮長期超標。
(2)為保證塔釜廢水中氨含量盡可能地達標,在現有分離裝置條件下,塔中濃氨水采出量則盡可能增加,由此造成濃氨水濃度下降,為后續氨精制開工造成較大困難;盡管在操作中為保證此中部濃氨水濃度,采取過增大回流的方案,但由于增大回流后,塔板易于液泛,該方案在操作中存在較大難度;塔中濃氨水采出量減小,還導致塔頂溫度升高,部分氨混入塔頂產品,在冷凝過程中形成銨鹽,易堵塞管道。
(3)進料廢水中除氨等易揮發組分外,還含有大量粉塵和焦油等固形物和高粘度組分,操作過程中浮閥塔板上以及塔釜再沸器中經常集灰和焦油,嚴重影響了塔板和再沸器的正常工況。
經過對上述問題的綜合分析,可以認為上述非正常運行狀態主要由于進料中的氨含量超出設計值,分離設備的分離能力不足和進料中固形物含量較大,塔板的氣液接觸形式不良2個主要原因造成。解決設備分離能力不足可采用增加分離塔板數的方法實現。解決固形物集聚的方法可以通過更換具備良好汽液接觸形式、抗堵防垢的內構件來解決,再沸器由于結垢物的特殊性可采用“兩開一備”的形式保證再沸器清灰不影響設備的正常操作。
原有粗氨水蒸餾塔為一變徑板式塔,塔板為F1型浮閥塔板。其中1~24層(自下而上)塔徑為2000mm,塔板為傳統弓形雙溢流塔板;25~30層塔徑為1200mm,塔板為傳統單溢流塔板。
氨含量為5000mg/L(其中游離氨濃度為4000mg/L,固定氨為800mg/L)左右的稀氨水以70t/h的流量進入粗氨水蒸餾塔第24層塔板,從塔中部第12層板采出濃度為12%的濃氨水。該裝置在實際運行中主要存在如下問題:
(1)原料廢水中氨含量受氣化所用煤質的影響經常超標,通常情況在5500~1000mg/L間波動,造成塔釜廢水氨含量經常在300~1000mg/L之間徘徊,嚴重影響了后續生化處理的操作,使生化處理排放水中氨氮長期超標。
(2)為保證塔釜廢水中氨含量盡可能地達標,在現有分離裝置條件下,塔中濃氨水采出量則盡可能增加,由此造成濃氨水濃度下降,為后續氨精制開工造成較大困難;盡管在操作中為保證此中部濃氨水濃度,采取過增大回流的方案,但由于增大回流后,塔板易于液泛,該方案在操作中存在較大難度;塔中濃氨水采出量減小,還導致塔頂溫度升高,部分氨混入塔頂產品,在冷凝過程中形成銨鹽,易堵塞管道。
(3)進料廢水中除氨等易揮發組分外,還含有大量粉塵和焦油等固形物和高粘度組分,操作過程中浮閥塔板上以及塔釜再沸器中經常集灰和焦油,嚴重影響了塔板和再沸器的正常工況。
經過對上述問題的綜合分析,可以認為上述非正常運行狀態主要由于進料中的氨含量超出設計值,分離設備的分離能力不足和進料中固形物含量較大,塔板的氣液接觸形式不良2個主要原因造成。解決設備分離能力不足可采用增加分離塔板數的方法實現。解決固形物集聚的方法可以通過更換具備良好汽液接觸形式、抗堵防垢的內構件來解決,再沸器由于結垢物的特殊性可采用“兩開一備”的形式保證再沸器清灰不影響設備的正常操作。
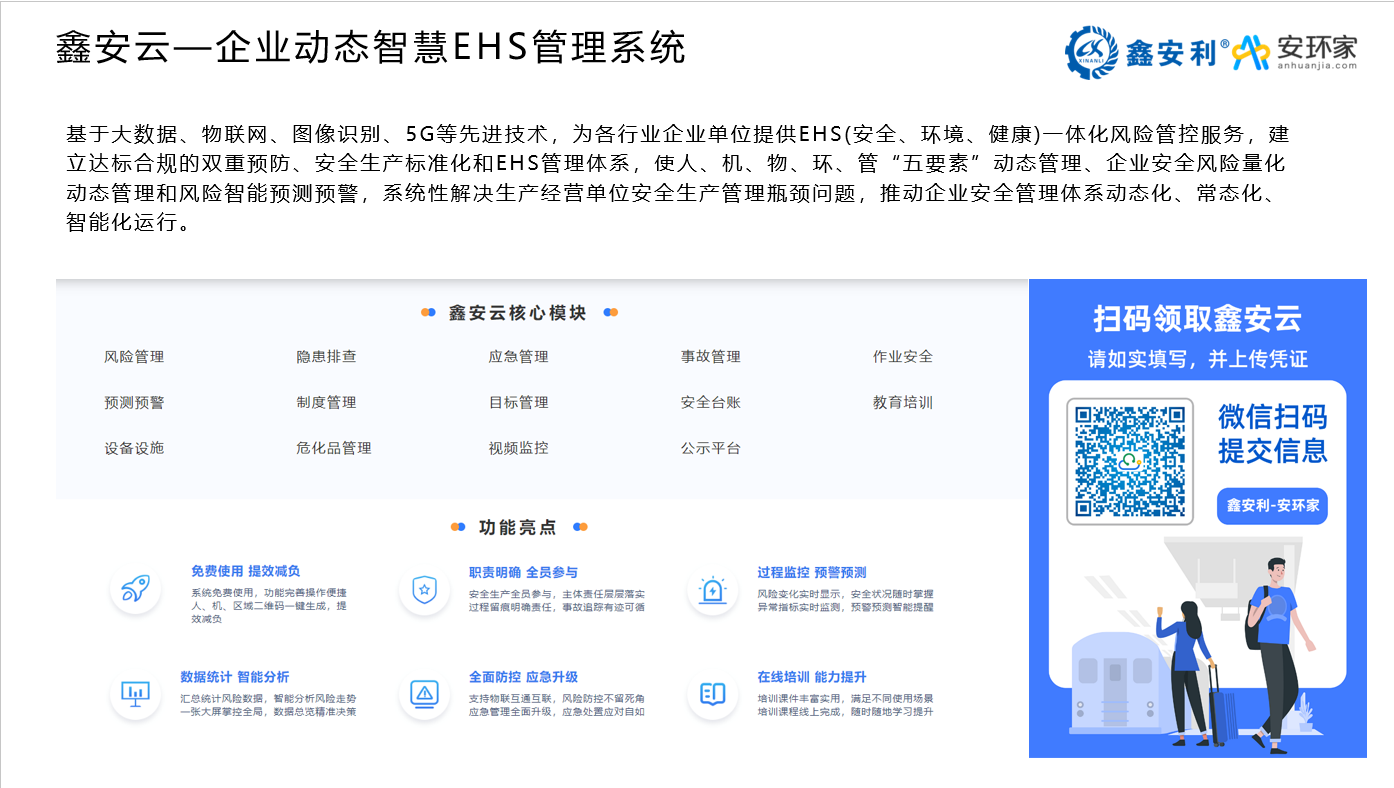